
Abrasive Blast Cabinets
Dry Abrasive Blast Cabinets
-
Optimized for Efficiency and Reliability
Engineered for continuous operation, high reliability, and adaptability—ideal for demanding cell production environments.Flexible, Space-Saving Design
Available in six compact models to accommodate various part sizes and workspace limitations, with a detached power module for added layout flexibility.Operator-Focused Ergonomics
Includes 17 ergonomic enhancements such as height-adjustable lift legs, quick-change glove ports, LED lighting, and centralized controls for ease of use.Low Maintenance and High ROI
Built for consistent results, simple operation, and reduced maintenance—delivering low cost of ownership and a fast return on investment.Advanced Dust and Maintenance Systems
Equipped with reverse-pulse dust collectors, auto-pulse cleaning, and differential pressure gauges to minimize downtime and streamline upkeep.
-
Clemco designs and builds engineered-to-order solutions for specialized parts handling—integrating automation, robotics, and enhanced interfaces to optimize your production process. Click Here to learn more.
Wet Abrasive Blast Cabinets
-
Precision Cleaning for Sensitive Parts
Delivers consistent, high-quality surface preparation ideal for delicate metals, electrical components, and complex geometries.Boosts Production Efficiency and Safety
Enhances throughput and operator safety with dust-free blasting, safety interlocks, and ergonomic controls like a foot pedal and pressure regulator.Durable, Compact, and Integration-Ready
Stainless-steel construction ensures long-lasting use, while a compact footprint allows seamless integration into high-volume production lines.Versatile Media and Reliable Performance
Compatible with glass bead and aluminum oxide media; powered by a BNP suction blast gun and sump-integrated diaphragm pump for smooth, consistent blasting.Easy Maintenance and Clear Operation
Features quick slurry dump, easy-access maintenance points, and a high-visibility window for efficient operation and minimal downtime.
-
Clemco designs and builds engineered-to-order solutions for specialized parts handling—integrating automation, robotics, and enhanced interfaces to optimize your production process. Click Here to learn more.
Light Abrasive Blast Cabinets
-
Eco-Friendly, Chemical-Free Cleaning
Uses lightweight plastic and bicarbonate media to eliminate the need for hazardous chemicals—ideal for environmentally conscious operations.Gentle Yet Consistent Surface Prep
Delivers high-quality, repeatable results on delicate surfaces without compromising part integrity.Optimized Media Recovery
Adjustable reclaim systems ensure efficient media use and reduce waste, contributing to lower operating costs.Clear Visibility and Operator Comfort
High-performance dust collection maintains a clean view and safe working conditions inside the cabinet.Flexible and Scalable Design
Available in multiple sizes and customizable configurations to support varied part dimensions and demanding production environments.
-
Clemco designs and builds engineered-to-order solutions for specialized parts handling—integrating automation, robotics, and enhanced interfaces to optimize your production process. Click Here to learn more.
Tumble Blast Cabinets
-
Automated, High-Volume Blasting
Delivers consistent, hands-free abrasive blasting that minimizes operator fatigue and maximizes production efficiency.Precision Finishing for Complex Parts
Provides uniform coverage and repeatable results across a range of part sizes, shapes, and materials—including complex geometries.Tailored Solutions for Every Application
Choose from Tumble Barrel (small batches), Tumble Basket (delicate parts), or Tumble Belt (heavy-duty, continuous runs).Clean, Efficient Operation
Equipped with reverse-pulse dust collectors, media reclaim systems, and intuitive controls for reliable, low-maintenance performance.Built for Demanding Industries
Trusted in aerospace, automotive, power generation, and medical manufacturing environments where consistency and throughput matter most.
-
Clemco designs and builds engineered-to-order solutions for specialized parts handling—integrating automation, robotics, and enhanced interfaces to optimize your production process. Click Here to learn more.
Proven Performance. Rugged Reliability.
Generations of Excellence Transforming Our World, Worldwide since 1949
•
Generations of Excellence Transforming Our World, Worldwide since 1949
•
Generations of Excellence Transforming Our World, Worldwide since 1949
•
Generations of Excellence Transforming Our World, Worldwide since 1949 • Generations of Excellence Transforming Our World, Worldwide since 1949 • Generations of Excellence Transforming Our World, Worldwide since 1949 •
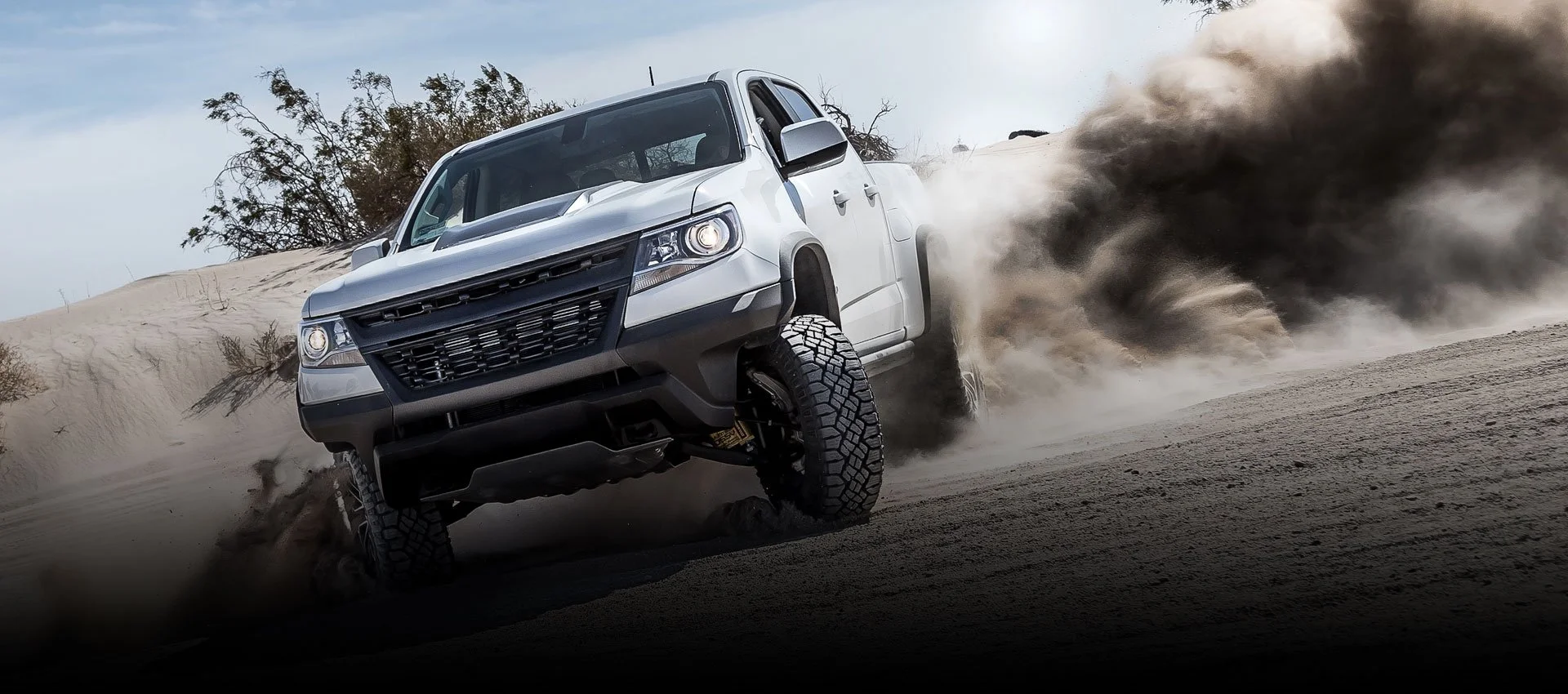