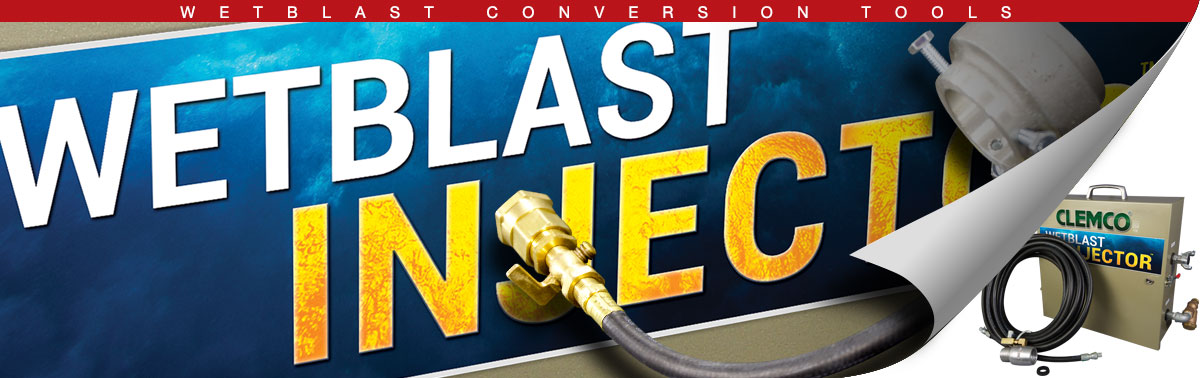
Wet blast Tools That Convert Dry-Blast Machines
Wetblast Injector System and Wetblast Attachment
You have dry-blast equipment that you rely on day in and day out, but you also miss out on jobs because your dry-blast equipment can’t wetblast. Perhaps you’re not ready to invest in a full-scale wetblast system—but you’d sure like those extra jobs. Clemco has two solutions:
- Wetblast Injector System – Converts a dry-blast machine into a high-performance wetblast system.
- Wetblast Attachment – Compact conversion tool for occasional wetblasting.
Wetblast Injector System
The only conversion kit on the market that modifies a dry-blast machine into a high-production wetblast system.
High-Performance Wetblast Capabilities
Take on any job that a full-scale wetblast system can:
- Water-adjustment controls at operator’s fingertips for precise fine-tuning of water flow into the blast stream.
- Water and media mix before entering the blast nozzle, which helps:
- Maintain high media exit velocity, ensuring efficient blasting.
- Fully saturate media with water, improving dust suppression for visibility and regulatory compliance.
- Ensure thorough wash down of blast surface for a contaminant-free finish.
Easy to Use
Quickly and easily available for any job:
- Compact and lightweight.
- Easy to transport and store because it takes up little space.
- Simple setup. Connect to:
- A compressed-air source.
- A pressurized, municipal water source such as an outdoor spigot or a kitchen faucet.
- Or use the water pump that comes standard with the Wetblast Injector to retrieve water from a storage tank.
Application Versatility
Switch back to dry blasting with the twist of a knob:
- Take on wet- and dry-blast jobs.
- No need to buy a second piece of equipment. The Wetblast Injector converts the dry-blast pot you already have into a complete wetblast system.
Compliance
Allows you to comply with environmental safety regulations and safeguard your operators from exposure to hazardous dust:
- Suppresses dust generated during abrasive blasting, reducing operator, co-worker, and bystander exposure to hazardous dust.
- Helps satisfy urban dust-abatement requirements when blasting in metropolitan areas.
- Decreases dust-containment and cleanup costs, saving you time and expense.
Specifications – Six Configurations
One Operator
- 1-1/4” nozzle adaptor
- 50 mm nozzle adaptor – 1-1/4” entry
- 50 mm nozzle adaptor – 1” entry
Two Operators
- 1-1/4” nozzle adaptor
- 50 mm nozzle adaptor – 1-1/4” entry
- 50 mm nozzle adaptor – 1” entry
Wetblast Attachment
For contractors who don’t wetblast every day—but need to be
ready for wetblast jobs.
Application Versatility
Wetblast capabilities quickly installed on your dry-blast machine at
a low upfront cost.
- Water-adjustment valve at operator’s fingertips for adjusting water flow into media after it exits the blast nozzle.
- Best suited for contractors who primarily dry blast but need wetblast capabilities in their back pocket.
Easy to Use
Quickly and easily ready for wetblast jobs:
- Simple to install and detach.
- Compact and lightweight. Could fit in your toolbox. Easy to store.
- Simple, low-maintenance design.
- Does not require an air supply.
Compliance
Allows you to comply with environmental safety regulations and safeguard your operators from exposure to hazardous dust:
- Suppresses dust generated during abrasive blasting, reducing operator, co-worker, and bystander exposure to hazardous dust.
- Helps satisfy urban dust-abatement requirements when blasting in metropolitan areas.
- Decreases dust-containment and cleanup costs, saving you time and expense.
Requirements for Operation
- Access to a pressurized, municipal water source such as an outdoor spigot or a kitchen faucet.
- Can also be connected to a water storage tank, but you need to supply the water pump.
Specifications – One Configuration
- Use with all standard nozzles except CT nozzles.
- Includes water ring, water-adjustment valve, flexible hose, and garden-hose fitting.
Wetblasting also is known as wet abrasive blasting, wet blasting, vapor blasting, slurry blasting, dustless blasting, and wet sandblasting. However, sand should never be used when wet or dry abrasive blasting because breathing abrasive containing crystalline (free) silica can lead to serious or fatal lung disease.