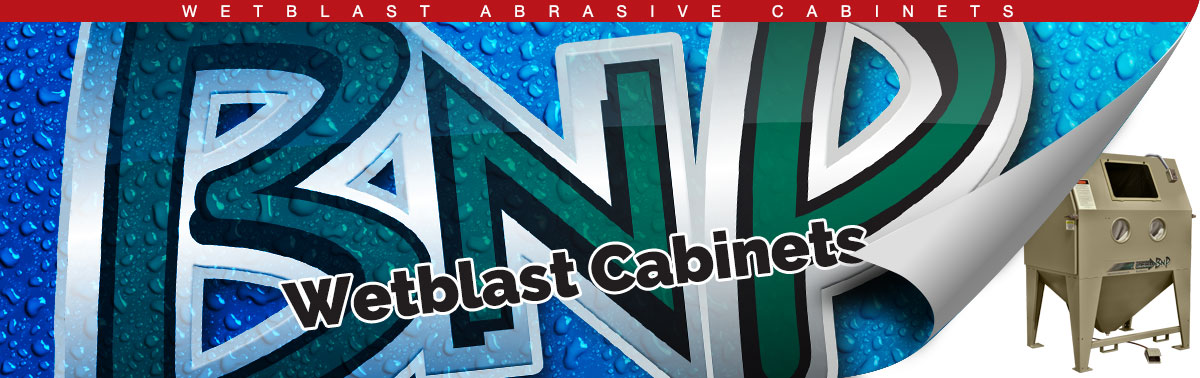
Wet blasting is an ideal method for achieving best results when cleaning and finishing sensitive metal surfaces, electrical components, and other delicate parts. The challenge is to deliver wet blasting operations efficiently, consistently, and safely, especially in high-volume production environments.
Our line of Wetblast Cabinets takes the inefficiencies and uncertainties out of surface preparation and delivers reliable productivity, performance, and operator safety.
Productivity
Production deadlines matter, and operators need wetblast equipment that delivers repeatable results when they’re needed. Our cabinets improve the productivity of wet blasting and provide:
- Easy access to routine maintenance components for minimal downtime.
- A quick and accessible slurry dump for easy clean-up and refreshing.
- Air regulators within easy operator reach to maintain ideal air pressure on the fly.
- Window cleaner for high visibility to ensure consistent blast coverage and prevent over-blasting.
Our BNP Weblast Cabinets come in two sizes, each with an option for use with glass beads or another for more aggressive media such as aluminum oxide:
- BNP 250 Wetblast Suction Cabinet: 36”W x 35”D x 37”H
- BNP 260 Wetblast Suction Cabinet: 50”W x 39”D x 43”H
Performance
When blasting sensitive and expensive components and parts, proper equipment operation is critical for preventing damage during blasting and getting the job done on time. Our wetblast cabinets offer numerous advantages to achieve quality performance including:
- A high-performance BNP suction gun.
- High-quality, stainless-steel construction for reduced wear and corrosion of equipment.
- Ideal ventilation for high visibility inside the cabinet.
- Consistent flow of the media/water mixture with sump-integrated diaphragm pump.
Safety
Blasting can be dangerous for both operators and parts unless the right precautions are taken. Dust in the air could be harmful for operators, and frictional heat, static build-up, or too aggressive of a blast can damage sensitive parts. Our Wetblast cabinets help negate these concerns with:
- Safety interlocks to prevent blasting while the doors are open to keep operators safe.
- Dust-free blasting to reduce operator exposure when cabinet is opened.
- Eliminates static electricity build-up generated by dry blasting.
- Pneumatic foot pedal for simple, ergonomic operation
Engineered Solutions
Wet blasting needs can vary greatly from customer to customer. We will work directly with you to develop customized solutions to meet your specific needs for blasting. Our goal is to strengthen the overall performance and efficiency of your production operations. Want to learn more?
Abrasive blasting (formerly known as sandblasting) also is called grit blasting, bead blasting, media blasting, soda blasting, dry blasting, sponge blasting, shot blasting, and shot peening. However, sand should never be used when abrasive blasting because breathing abrasive containing crystalline (free) silica can lead to serious or fatal lung disease.