Engineering Customized Solutions for Unique Abrasive Blasting Challenges
Perhaps your application necessitates specialized part handling or movement, or it is unusually complex. Maybe you’re unsure how much automation you need—if any—or even robotics. And whatever the solution, it needs to optimize your entire production process. No upstream or downstream disruptions.
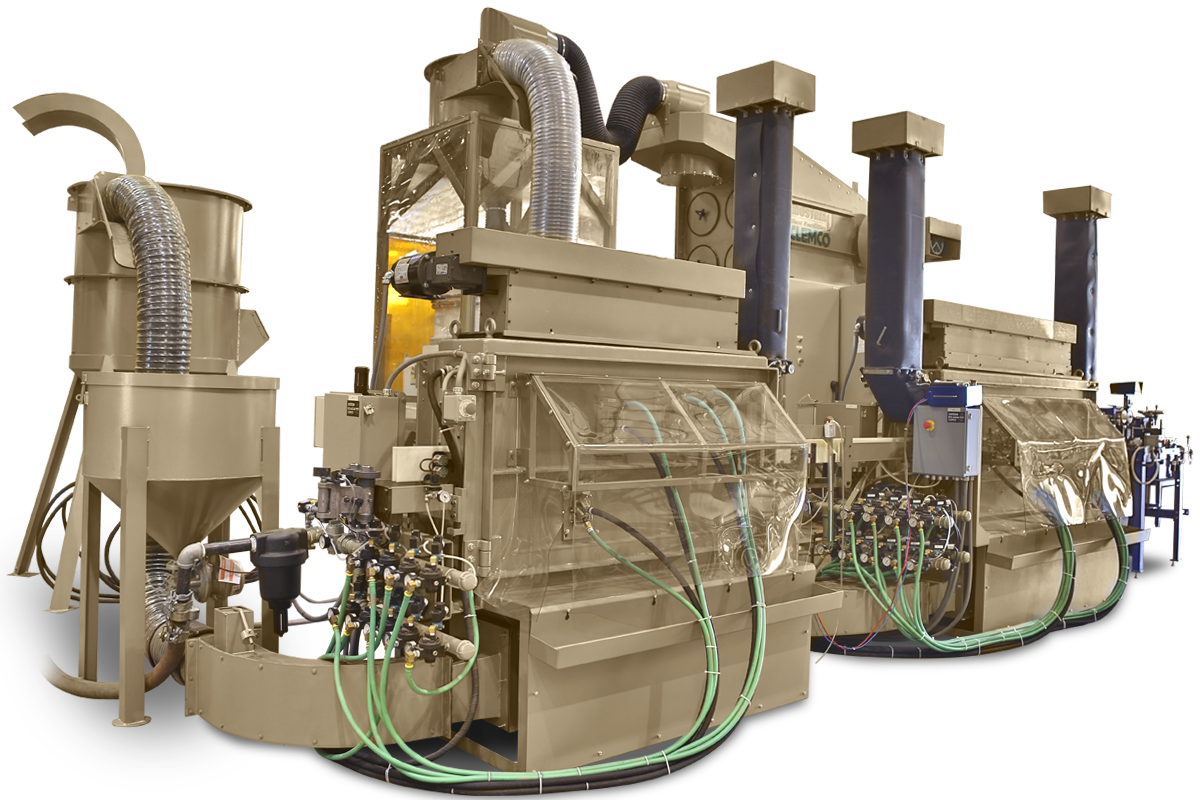
Clemco is your partner when it comes to engineering solutions for your abrasive blasting processes because we understand that off-the-shelf equipment doesn’t cut it for specialized surface preparation applications. We are with you for the entire process, leveraging the design, fabrication, project management, and production capabilities of our U.S. engineering and manufacturing facility—to ensure you get the customized solution that increases the productivity and profitability of your entire manufacturing operation.
Clemco Is with You from Start to Finish—Every Step Of the Way
The Solution: Ideation to Realization (I2R™)
Experience —After more than 80 years of helping aerospace, medical, firearms, energy production, manufacturing, and other clients implement solutions for their abrasive blasting operations, Clemco has refined its solution-design methodology: Ideation to Realization (I2R™).
Collaboration —During the six-phase I2R process, Clemco engineers collaborate with your team to uncover the true root cause or causes of your challenges, wherever they may be, perhaps even upstream or downstream of your abrasive blasting operation. We may discover solutions that you had never conceived of—and that may be less expensive to implement. We dig deep for a solution that not only addresses the obvious issues—which often are symptoms of the underlying causes—to find a solution that solves problems beneath the problem.
Value —Clemco is not your typical quote-it, deliver-it, and forget-it vendor. In partnership with you, we fix the problems on all levels and manage the project every step of the way so that you get a true long-term solution that delivers a verifiable return on your investment. Clemco partners with you—from Ideation to Realization.
Step 1: Needs Assessment
Engineering the right solution requires collaboration with your team to discover the challenges impacting your abrasive blasting applications.
- Clemco engineers apply a systems approach to understanding how your blasting applications integrate upstream and downstream in your process flow.
- We clarify your goals for cost savings, quality improvement, regulatory concerns, and increased productivity.
- We explore options for overcoming the challenges—perhaps some you never considered that might even be less expensive.
- The Discovery Step may occur virtually and/or onsite. Clemco takes the approach that works best for your team.
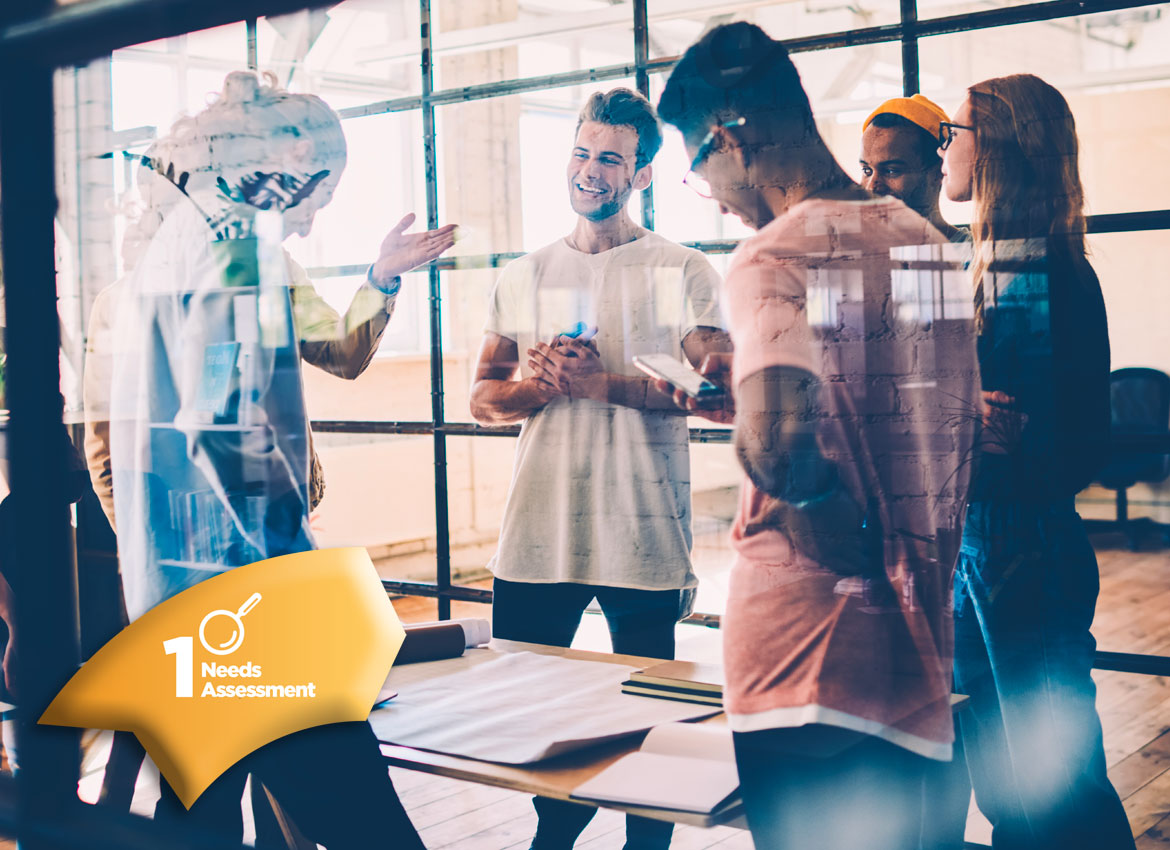
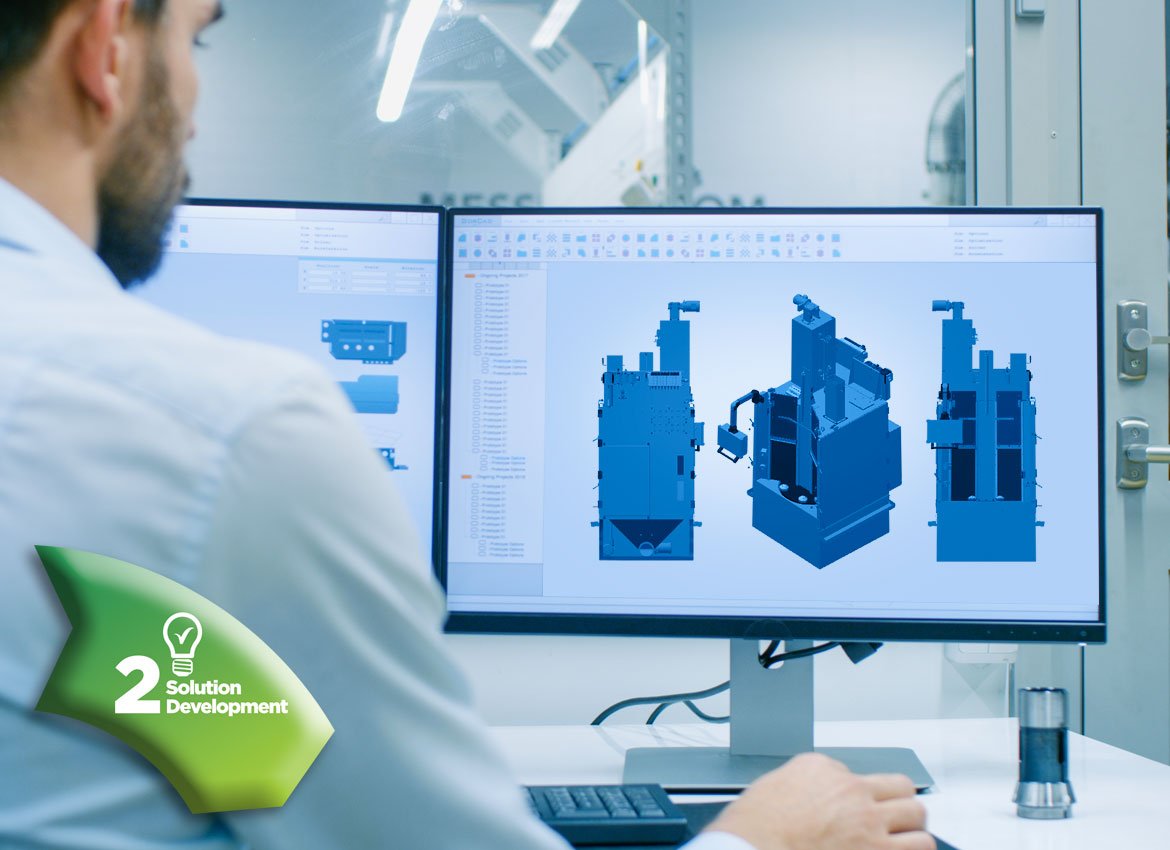
Step 2: Solution Development
Clemco project managers and engineering analyze possible solutions and then ideate with your engineers and/or team members to develop possible approaches. They continue to collaborate “engineer-to-engineer” until the best solution is identified.
- Your team and Clemco investigate whether new discoveries have altered the scope of your project.
- We collaboratively determine the best concepts to further evaluate, which may include blasting sample parts to gather data in Clemco’s in-house Sample Processing-R&D Lab.
- After analyzing all data, the Clemco engineering team will recommend the solution that best satisfies your criteria, in addition to clarifying timelines and costs.
- Clemco continues to refine, with your input, the best-possible solution until all parties approve a final design.
Step 3: System Build
Clemco utilizes its in-house fabrication, welding, assembly, automation integration, and manufacturing expertise to build your engineered solution.
- Clemco engineers integrate the electronic controls and diagnostics, automation options, and/or robotic technology that you have selected for your engineered solution.
- As a Rockwell Automation Silver OEM Partner, KUKA automaton provider, and a Fanuc Robotics Authorized System Integrator, Clemco expertly integrates any requested automation and/or robotics.
- We rigorously test and refine your blasting solution at our in-house manufacturing and engineering facility.
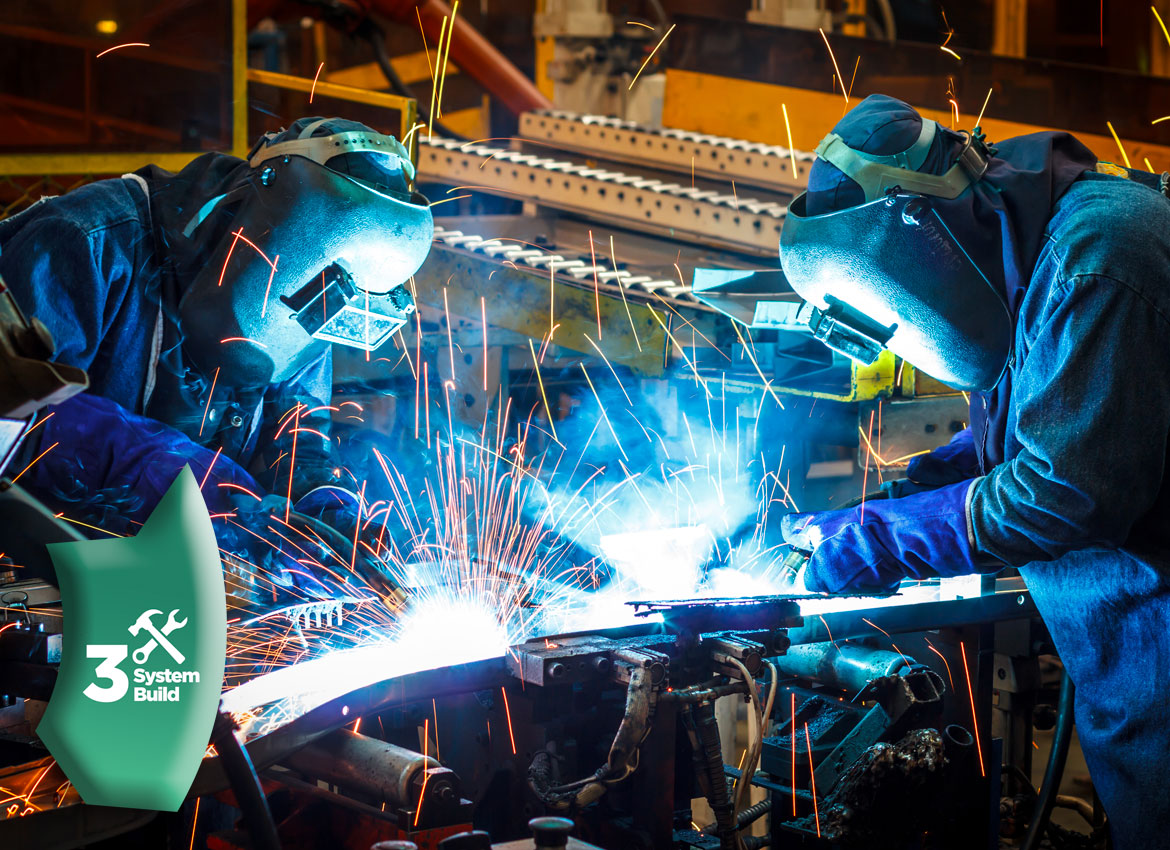
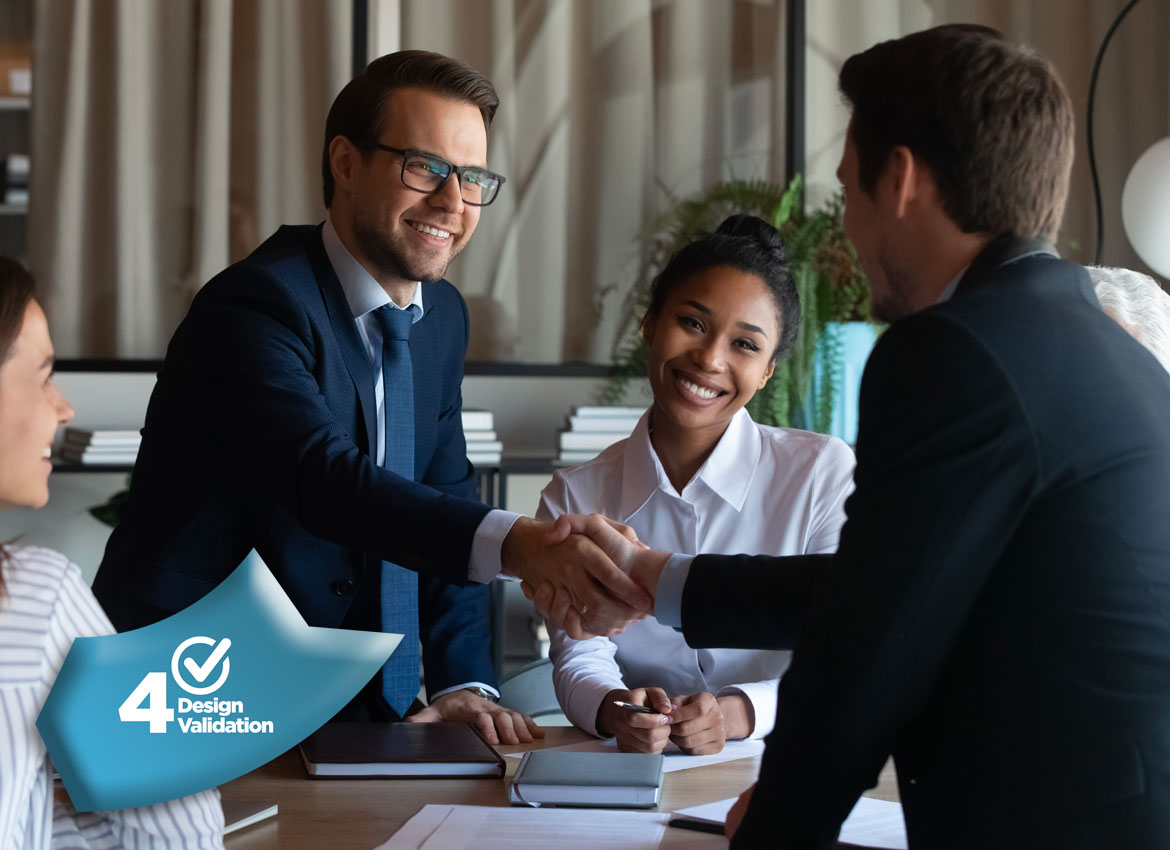
Step 4: Design Validation
Clemco invites your team to attend, in-person or virtually, a run-off test at our manufacturing facility. Your team and Clemco identify modifications needed, if any, to your equipment so that it meets your design requirements.
- At the run-off test your engineered equipment abrasive blasts parts that you have provided under the variables and conditions you want tested.
- Your team and Clemco identify issue to resolve, if any, with your engineered solution.
- We also agree upon the baselines parameters for Clemco to set on your equipment.
- If modifications are required, Clemco makes the required changes and retests the equipment to ensure it operates per your specifications, keeping your team in the loop during the entire process.
- Upon your approval, we schedule delivery of your engineered solution to your facility.
Step 5: Startup
A Clemco technician travels to your facility to supervise your equipment’s initial startup. This visit is inclusive with your Clemco Engineered Solution.
- The technician inspects your team’s already completed installation of its engineered solution.
- The technician then supervises the startup of your engineered solution.
- The technician also instructs supervisors and operators on proper maintenance, operation, troubleshooting, and proper settings for the equipment.
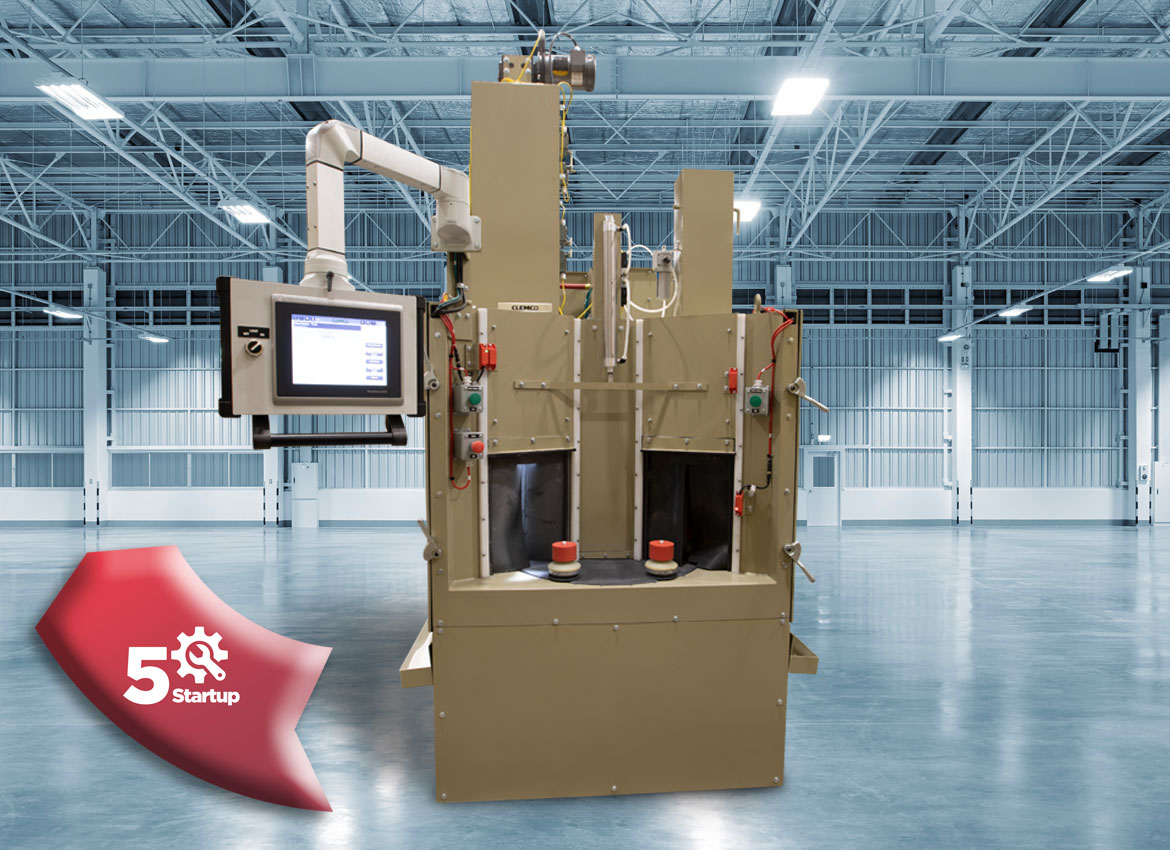
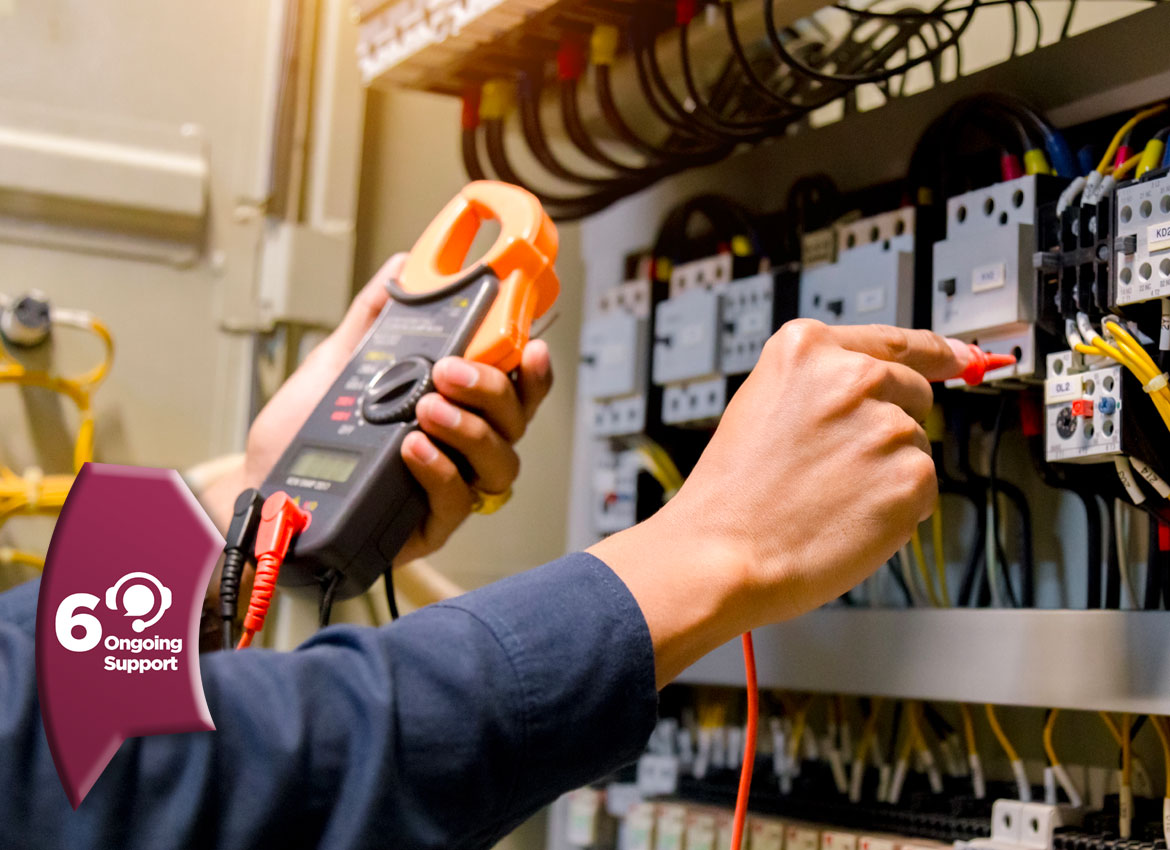
Step 6: Ongoing Support
Clemco provides end-to-end support for your custom-engineered abrasive blasting solution, assuring that your capital investment delivers the results and payback you expect.
- Project management professionals manage the entire project to keep it on time and on budget.
- Technical service personnel provide initial training and ongoing telephone support for maintenance and operation questions.
- Onsite field service is available for troubleshooting, maintenance, and repairs.
For More Information
If you’re eager to learn more, simply complete the brief form below and our team of knowledgeable experts will be in touch with you. We sincerely appreciate your interest and look forward to connecting with you soon.
Abrasive blasting (formerly known as sandblasting) also is called grit blasting, bead blasting, media blasting, soda blasting, dry blasting, sponge blasting, shot blasting, and shot peening. However, sand should never be used when abrasive blasting because breathing abrasive containing crystalline (free) silica can lead to serious or fatal lung disease.