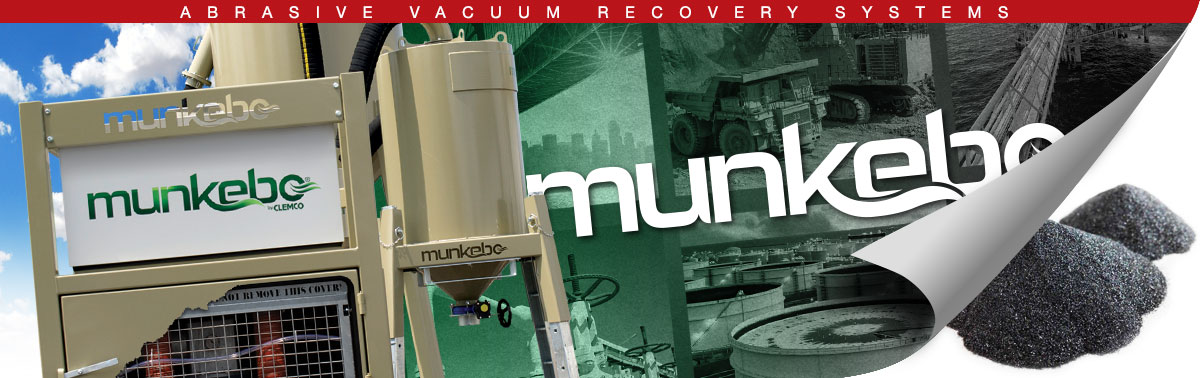
Your abrasive recovery just got quicker and easier.
Removing spent abrasive for disposal or recycling is a pain. And when it takes too long, it eats away your time and profits. In fact, cleanup after a blasting job can run up to 40% of a project’s total cost. Munkebo Portable Abrasive Vacuum and Recovery Systems make recovering spent abrasive quick and easy, saving you time and money.
Productivity and Performance: Think of Munkebo Abrasive Vacuum Systems as giant vacuum cleaners. Their recovery hoses easily get to where abrasive is lodged or hidden—places that would be nearly impossible to recover abrasive from with manual or mechanical methods—and Munkebo Systems are faster!
Versatility: Easy to Stage, Transport, and Configure: Munkebo Systems have modular designs, forklift pockets and lifting eyes on all major components, smaller footprints, and lighter weight because they are powered by electric motors. So they are easier to transport, stage, and arrange into different configurations on job sites.
Durability and Convenience: Munkebo Systems are built to last. Our business is not based on replacement parts sales—it is based on manufacturing durable, reliable, low-maintenance equipment that is easy and convenient to use. Our equipment will age better than you.
Munkebo Vacuum Operations Guide
[arve url=”https://vimeo.com/857174933?share=copy” title=”Munkebo Vacuum Operations Guide” mode=”lightbox” loop=”no” muted=”no” /]
Munkebo MB 3000 Demo
[arve url=”https://vimeo.com/847096765?share=copy” title=”Munkebo MB 3000 Demo” mode=”lightbox” loop=”no” muted=”no” /]
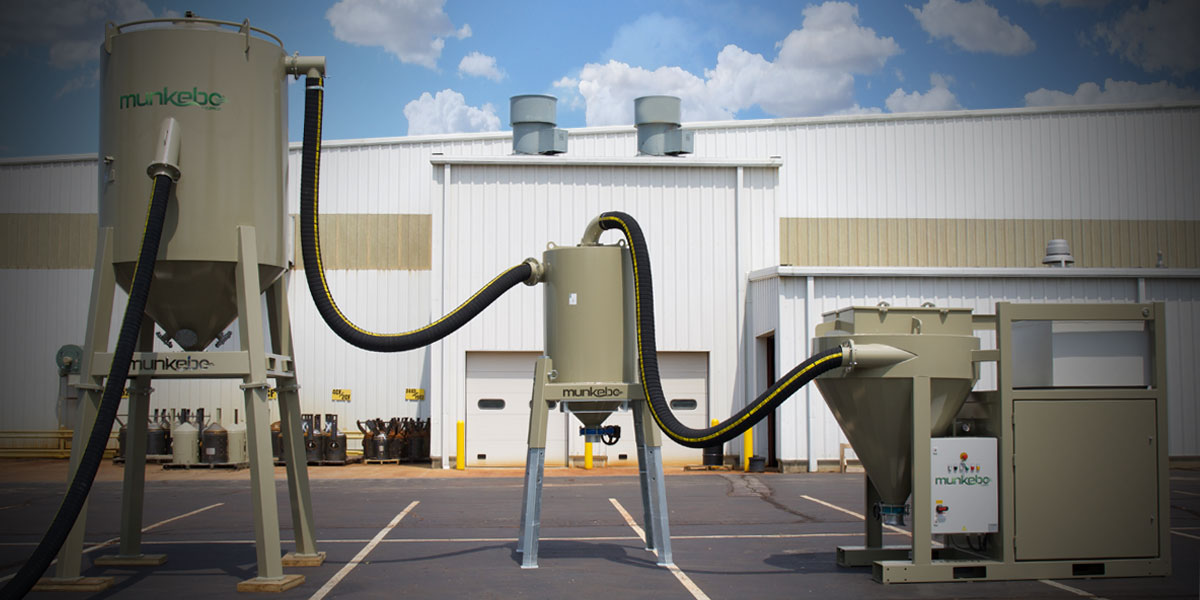
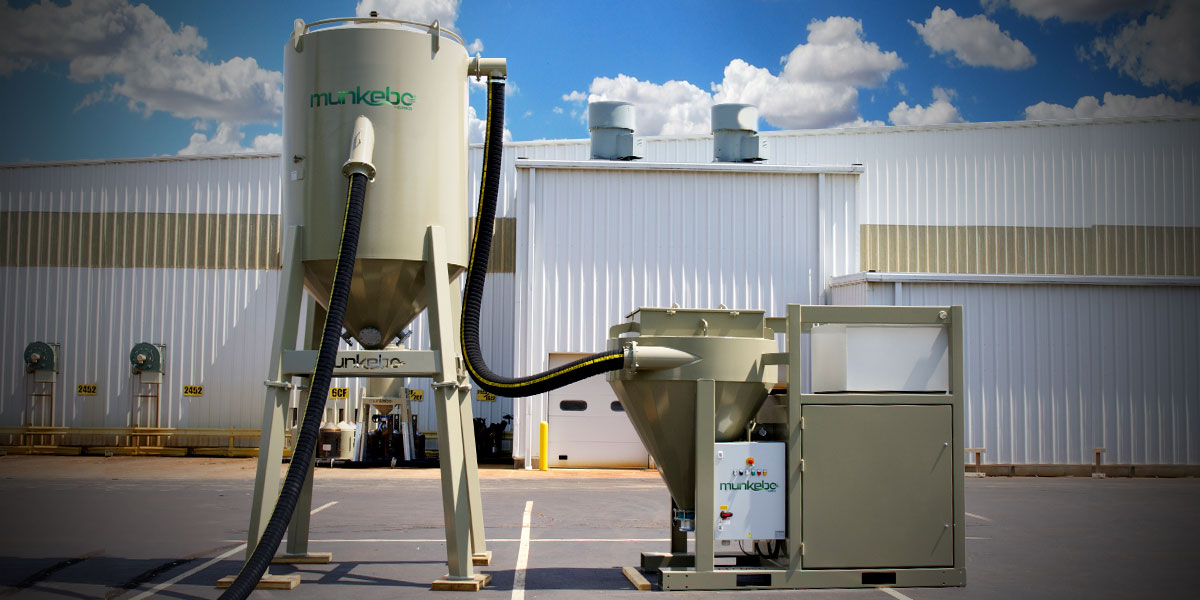
Increase Productivity
The Problem
- Manual shoveling, scooping, and sweeping is time-consuming, backbreaking work—and highly inefficient. It’s impossible to get all media out of corners, cracks, and other hard to reach areas, which also can lead to safety and compliance issues.
- Mechanical equipment wears out quickly, leading to costly repairs and unexpected downtime.
Munkebo’s Solution
- Put simply, a Munkebo Abrasive Vacuum System is like a giant vacuum cleaner. Its recovery hose easily gets to where abrasive is lodged or hidden—places that otherwise would be nearly impossible to recover abrasive from—and Munkebo Systems are faster.
- Pneumatic conveyance and gravity move abrasive through a Munkebo System. This design speeds up abrasive recovery and reduces the number of mechanical parts in a system.
The Benefits
- Operators recover more abrasive in less time—increasing your productivity and profit.
- You spend less on equipment repair and maintenance, and have less unexpected downtime.
Versatility That Fixes Problems
The Problem
- Space is limited on job sites.
- Access to job sites is obstructed or difficult.
- Equipment may have to be placed far from spent abrasive.
- Equipment is heavy and has a large footprint, making it difficult to transport, stage, and arrange into different configurations.
Munkebo’s Solution
-
Munkebo Systems have a small, modular design.
-
Each major component is equipped with forklift pockets and lifting eyes.
-
The systems are powered by electric motors that weigh less than diesel engines.
-
Depending on the system, Munkebo equipment can be placed as far as 80 ft to 1,300 feet from spent abrasive.
The Benefits
- Munkebo Systems are simpler and easier to fit into the space restrictions of a job site.
- Their modular designs, forklift pockets and lifting eyes, and smaller footprints, and because they weigh less than diesel-powered recovery systems, make Munkebo Systems easier to transport, stage, and arrange into different configurations.
- Likewise, Munkebo Systems are easier to load and unload on standard over-the-road trailers.
- With a Munkebo System, you can take on more jobs at a greater variety of locations, allowing you to quickly realize a return on your investment.
Durability and Convenience That Simplifies the Job
The Problem
Abrasive recovery equipment often breaks down and is difficult to operate and learn, which all costs you time, money—and other jobs.
Munkebo’s Solution/Benefits
Our business is not based on replacement parts sales—it is based on manufacturing durable, reliable, low-maintenance equipment that lasts over time and is easy to use. All steel construction, along with rugged hoses and components, are all designed for low wear, infrequent replacement of parts, and little routine maintenance. Our equipment will age better than you.
Solution: Dust-Collector Filter Cartridges
Benefits:
-
- Automatically cleaned every minute by a reverse-pulse jet of air.
- Simplifies cartridge maintenance, ensures consistent cartridge cleaning, and prolongs service life.
Solution: Hoses Connect Inside Inlets
Benefit:
-
- Significantly reduces coupling wear.
Solution: Durable, Reinforced Hoses
Benefits:
-
- Composed of two flexible, polyester layers with antistatic copper wire embedded between them.
- Hoses are strong enough to withstand extreme vacuum pressure.
Solution: Adjustable-Height Legs
Benefits:
-
- On recovery storage hopper and optional cyclone precleaner.
- Allow for different configurations of equipment.
Solution: Emergency Stop Button
Benefit:
-
- Stops or reduces a hazard that could damage equipment and/or injure operators.
Solution: Electric Control Panel
Benefits:
-
- Indicator Lights: Power On/Off, system failure, and butterfly-valve open.
- Buttons: Start, stop, and emergency stop.
- Circuit Breaker
Regulations for Media Cleanup and Disposal Are Increasing
The Problem
- Manual and mechanical media cleanup creates respiratory hazards by stirring dust into the air, which can lead to safety and compliance issues.
- Likewise, it’s impossible to get all media out of corners, cracks, and other hard to reach areas with manual cleanup or mechanical systems, which also can lead to safety and compliance issues.
-
Failure to comply with regulations results in fines and loss of business.
Munkebo Solution
-
Munkebo Systems remove dust when they recover spent media, reducing respiratory hazards.
-
They also can be used solely for vacuuming up dust.
- Munkebo Systems are more efficient at recovering media than manual cleanup or mechanical systems.
The Benefits
-
Reduces operator exposure to respiratory hazards
- Reduces regulatory compliance costs.
- You are less likely to lose business because of safety and/or compliance issues.
Electric Motors That Perform
Smaller and Lighter
-
Munkebo electric motors weigh less and have a small footprint, which allows for the equipments’ smaller modular design.
-
This reduction in weight and size allows for greater flexibility in how and where equipment can be staged and arranged.
Simple to Maintain
-
Removable motor mounts make it simple to remove the full motor if service is needed.
-
Few moving parts reduce the number of wear components and maintenance costs.
-
A top-mounted terminal box simplifies electrical troubleshooting and repairs.
-
A thermal overload relay shuts down the electrical system if it overloads, protecting the motor from burning out.
-
A safety relief valve releases excessive pressure, which helps keep the motor from overheating.
Clean and Quiet
-
Munkebo electric motors are oil and diesel free, so they run cleaner and emit no exhaust.
-
They are quiet. The vacuum unit produces noise levels at or below 85 dBa at 3.3 ft, which is below the OSHA standard.
-
The vacuum pump is belt-driven, and its 3-lobe, positive displacement technology is quieter and has fewer vibrations than 2-lobe systems.
Powerful and Effecient
- Munkebo electric motors are more efficient and cost less to run.
- For example, the 75 kW electric motor in Munkebo’s MB-3000 System produces as much power an a typical 110 kW diesel engine.
It’s a Simple Design
Adaptable, Flexible Equipment
Munkebo Systems have a simple, modular designs with only three major components that are easy to transport, stage, and arrange into different configurations on job sites.
Three Major Components
- Vacuum Unit: Includes integral dust collector.
- Abrasive Storage Hopper: Stores recovered media.
- OPTIONAL Cyclone Precleaner:
-
-
Extends the life of the dust collector cartridges and provides extra storage for dust and other carryover.
-
Recommended when recovering expendable and recyclable abrasives that produce high level of fines and dust.
- A Precleaner IS Needed When Using: Coal slag, nickel slag, and other dusty abrasives.
- A Precleaner Is NOT Needed When Using: Steel grit and other low-dust abrasives.
-
Three Smaller Components
- Hoses
- Hose Clamps
- Suction Nozzle
Six Systems: Choose the Right System for You
Pick Your System: Estimated Recovery Rates
Use the chart below to determine which of the six Munkebo Systems meets your recover-rate needs.
Hose dimensions affects recovery speed. Larger vacuum units need larger dimension hoses. The chart’s recovery rates are based on optimal conditions.
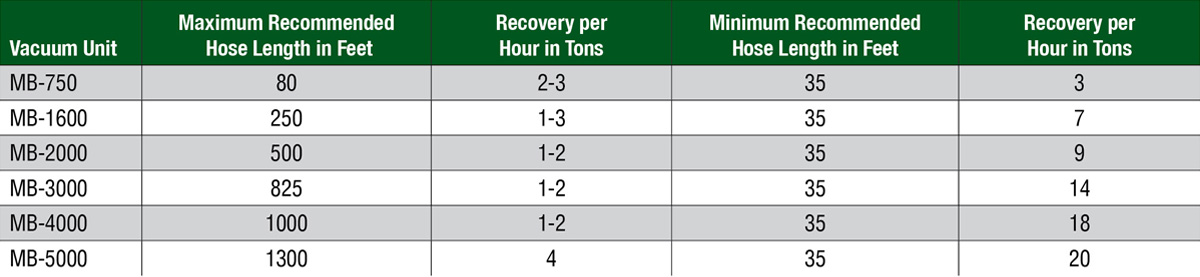
Case Studies
Contractor Purchases Nearly 30 Tower Systems Over 30 Years—All Still in Use
Your job site has limited space? Munkebo equipment’s small footprint and flexible, modular design enable you to use, or not use, system components as needed and to rearrange configurations to fit the space restrictions of your work area.
Abrasive blasting (formerly known as sandblasting) also is called grit blasting, bead blasting, media blasting, soda blasting, dry blasting, sponge blasting, shot blasting, and shot peening. However, sand should never be used when abrasive blasting because breathing abrasive containing crystalline (free) silica can lead to serious or fatal lung disease.