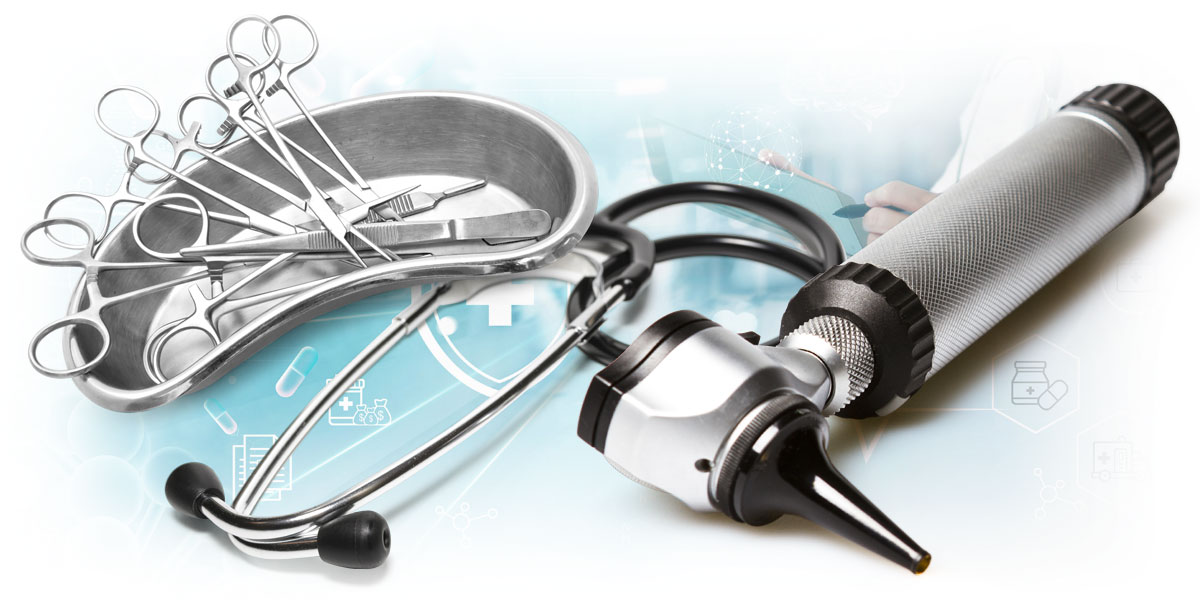
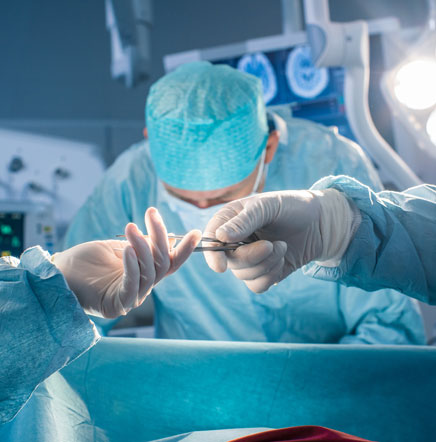
CASE STUDY 1:
Manufacturer Achieves 3X Production Rate with Automated Blasting System
A manufacturer of stainless steel laparoscopic surgical tools wanted to improve efficiencies in their finishing operation. Their instruments were machined and came from the fabrication shop with burrs, small defects, surface oxide, and slight discoloration. …
Manufacturer Achieves 3x Production Rate with Automated Blasting Solution for Surgical Tools
Problem: A manufacturer of stainless steel laparoscopic surgical tools wanted to improve efficiencies in their finishing operation. Their instruments were machined and came from the fabrication shop with burrs, small defects, surface oxide, and slight discoloration. With a production volume about 4,000 pieces per week, they needed to process at a rate of one finished part every 10 seconds.
Their finishing objectives included deburring and cleaning to remove oxidation and other contamination from the parts. Their manual process included sanding and wire brushing. A routine step also involved visually inspecting each finished part with a magnifying glass, a painstaking process.
Attention to detail and a fine finish were required to meet the demands of their medical community customer base, not to mention outshining their competition.
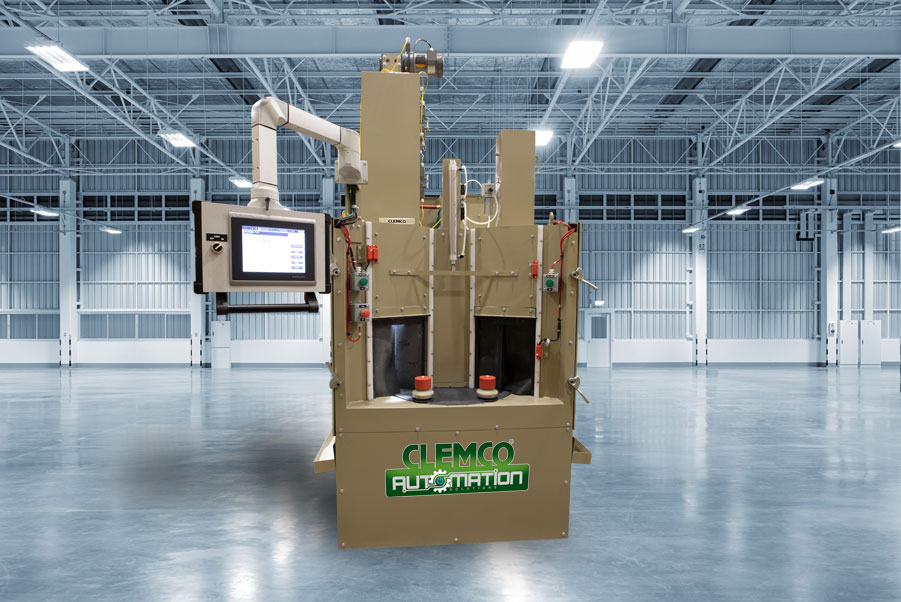
Solution: We offered to run parts for them to demonstrate how blasting could contribute to improving their operation and the customer took the distributor up on his offer. The surgical instruments were processed with No. 10 glass bead in suction-style (venturi-style) blast cabinet.
To the uninitiated, blasting is like magic. The customer purchased a manual cabinet. And not only were they able to achieve their production rate, but also, they saw an improvement in the quality of their parts. Glass bead blasting quickly and easily removed the burrs and oxidation and produced a matte finish, which was an unexpected but pleasant surprise. As you know, surprises in a manufacturing environment usually are not desirable! To the manufacturer’s delight, their customers raved about the matte-finish it served to eliminate the reflective glare on the instrument from the operating room’s high-intensity lighting, an obstacle they had lived with for years. Removing the shine from the instruments’ surface instruments increased surgical productivity.
With this value-added feature, tool production demand increased, and the manufacturer turned to Clemco once again for advice. This time, with challenging new requirements. They wanted to double their production to two parts every ten seconds.
Automating the blasting process involves careful assessment of the parts to be finished, the finishing objectives, any material properties or characteristics of the part that would dictate special handling, as well as consideration for the space and environment where the equipment will be used in the customer’s facility.
In this instance, the customer needed a machine that would speed the process so that production could be ramped up to meet greater demand. They wanted finished parts with a single process and an easy operational learning curve for the workers. They needed a reliable, easy-to-maintain machine that would run 24hr. if need be.
The parts had to be handled individually and lent themselves to an indexing turntable machine, in which parts are loaded individually onto a fixture and blasted one or two satellite stations at a time. In this application, the customer loaded three parts on one fixture, indexed to send the parts inside the cabinet for blasting, while they removed and reloaded more parts.
The finishing specification called for uniform coverage over 360 degrees around the part. In some medical applications, such as implants, specific roughness average (Ra) finishes are required. In this application, however, the goal was a visually acceptable part. The machine was fitted with eight blast guns and the same No.10 glass bead that was used in their manual blast operation was also used here.
To achieve the customer’s finishing goals, we created special fixtures designed to hold three parts per fixture. By loading three parts on each fixture, three parts could be completed every ten seconds and the finishing production rate tripled the original manual-process rate, giving the customer room to grow into the machine with increasing demand. For the time being, the additional finishing capacity allowed them to process several different size tools with a simple change-out in fixtures. The automated process assures repeatability, which contributed to greater time and cost savings by reducing the visual inspection rate and virtually all part reworks.
The challenge had been to design a machine and process that would offer a simple, elegant solution at a price that was within the customer’s budget. Solving customer problems are never a slam-dunk. In this project, with a combination of luck, and of course skill and expertise (I), the customer was thrilled with their investment in a simple automated process, with achieving triple their production rate, and with the assurance that they would not very soon outgrow the machine. Their business continues to grow, and, in their eyes, we shined.
Abrasive blasting (formerly known as sandblasting) also is called grit blasting, bead blasting, media blasting, soda blasting, dry blasting, sponge blasting, shot blasting, and shot peening. However, sand should never be used when abrasive blasting because breathing abrasive containing crystalline (free) silica can lead to serious or fatal lung disease.