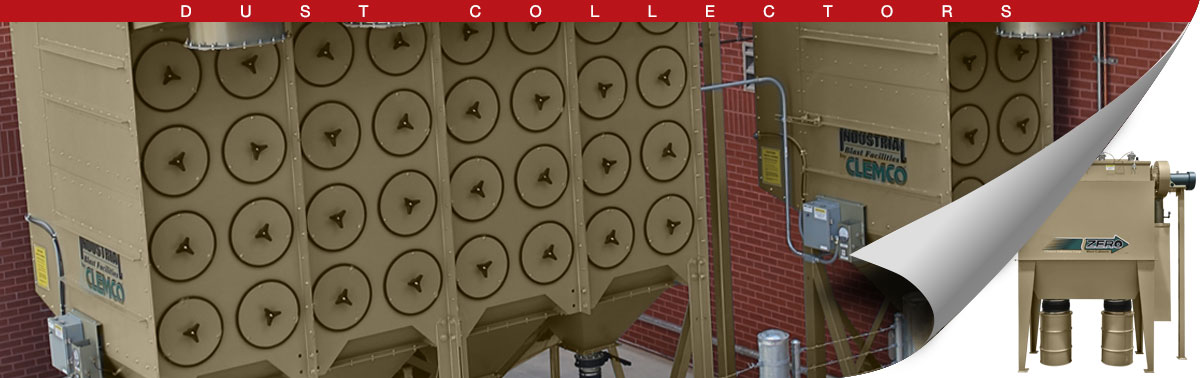
LPDC
You abrasive blast in a room or cabinet for two main reasons: dust containment and media recovery.
- Low ceiling? No Problem!
- Side or Top-mounted blower
- Side-loading double-latched filter door
- Feel the pressure
- Improved blower performance for better dust collection and reclaim
- Go with the flow
- Choice of 300/600/900 CFM fans to fit your application
- Don’t get tilted
- Fits upright thru most standard interior doors!
- 78H x 29W x 29D (not including fan)
Clemco offers three lines of dust collection solutions, all designed and manufactured in-house, to meet the requirements of your abrasive blasting operation while ensuring high productivity and a safe work environment.
Dust Collectors for Blast Cabinets to Achieve Better Ventilation and Media Recovery
A Dust Collector Not Optimized to Your Blasting System Can Choke Productivity, Profits, and Safety
You abrasive blast in a room or cabinet for two main reasons: dust containment and media recovery. But if your dust collector isn’t tailored to your blasting operation, you’re inviting productivity, maintenance, and safety issues:
- Compromised Visibility = Lower Productivity – Excessive dust compromises operator visibility to the point that blasting coverage and consistency can suffer.
- Hazardous for Operators and Other Employees – Even if blast room operators are wearing proper personal protective equipment (PPE), excessive dust is a respiratory hazard. Dust also is a hazard for coworkers near a blast room if it escapes. Likewise, dust that escapes from a blast cabinet is hazardous for operators and nearby coworkers.
- Degrades Media Working Mix – Dust collection is critical for productive media recovery. Efficient removal of dust, debris, and fines helps ensure that your media working mix is comprised of cleaned, properly sized media that keeps productivity high and blasting results consistent.
- Fines, Downtime, Maintenance Expenses – Effective dust collection helps you avoid fines from inspectors, as well as downtime and maintenance expenses resulting from wear caused by excessive dust.
For these reasons, Clemco offers three lines of dust collection solutions, all designed and manufactured in-house, to meet the requirements of your abrasive blasting operation while ensuring high productivity and a safe work environment.
CDF Dust Collectors – For High-Volume Blast-Room Ventilation and Large Recovery Systems
CDF Dust Collectors are engineered for large airflow applications such as ventilating blast rooms or for supplying the airflow to large M-Section Recovery Systems. Their robust design is ideal for outdoor installation, or indoors if desired. They frequently are incorporated into blast room solutions.
- Simple Cartridge Maintenance – CDF Dust Collectors have tool-less filter cartridge changeout and easy horizontal cartridge access. Horizontal access also saves floorspace because of its vertical stacking.
- High Efficiency, Long Service Life – CDF Dust Collectors have automatic, reverse-pulse operation, which means cartridges automatically self-clean. Consistently cleaned cartridges promote dust collector efficiency and filter longevity.
- Straightforward Waste Disposal – Easy access, 55-gallon waste drum for dust disposal.
- Quick, Flexible Installation – CDF Dust Collectors consist of bolt-together subassemblies, simplifying installation.
- CFM Options – Modular design allows for banks ranging in size from 4,000 CFM to 88,000 CFM, and additional banks can be added.
RPH Dust Collectors – For Intermediate Airflow Requirements
RPH Dust Collectors are frequently paired with blast cabinets, M-Section Recovery Systems, and air-wash abrasive cleaners (AWACs).
- High Efficiency, Long Service Life – RPH Dust Collectors have automatic, reverse-pulse operation, which means cartridges automatically self-clean. Consistently cleaned cartridges promote dust collector efficiency and filter longevity.
- Straightforward Waste Disposal – Easy access, 30-gallon or 55-gallon waste drum (depending on model) for dust disposal.
- Quick, Flexible Installation – RPH Dust Collectors consist of single-piece construction or bolt-together subassemblies on larger units, simplifying installation.
- CFM Options – Range in size from 600 CFM to 3,600 CFM to fit most cabinet and recovery applications.
CDC Dust Collectors – Economical Option for Lower-Volume Airflow Requirements
CDC Dust collectors are most often paired with medium to small-size manual blast cabinets.
- High Efficiency, Long Service Life – CDC Dust Collectors have manual, pushbutton operation and optionally can be upgraded to an automated, timed pulse. Consistently cleaned cartridges promote dust collector efficiency and longevity.
- Compact Design – Small footprints with a single, vertical filter fit into various industrial layouts.
- CFM Options – Range in size from 300 CFM to 900 CFM to provide an economical dust collection option for hand cabinets.
Abrasive blasting (formerly known as sandblasting) also is called grit blasting, bead blasting, media blasting, soda blasting, dry blasting, sponge blasting, shot blasting, and shot peening. However, sand should never be used when abrasive blasting because breathing abrasive containing crystalline (free) silica can lead to serious or fatal lung disease.