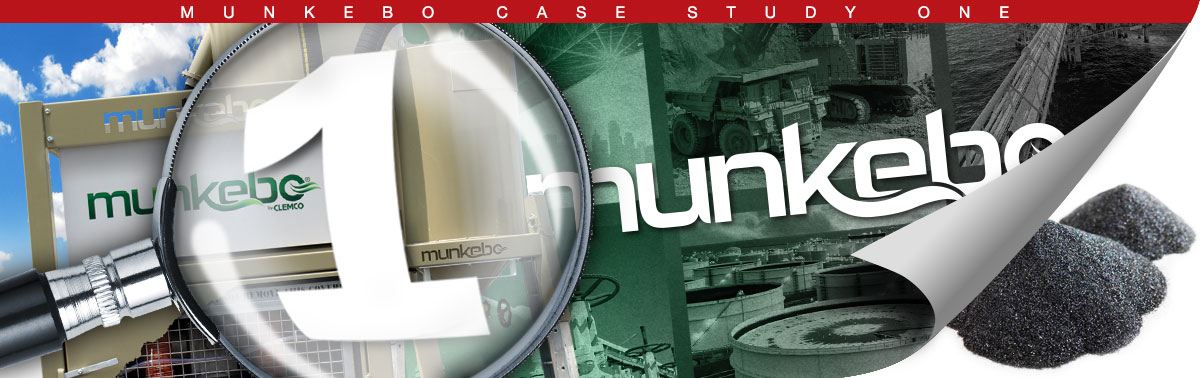
Water (and media) Under the Bridge
PROBLEM
In 2018, a Munkebo customer of 15 years needed to recover and recycle spent steel grit while blasting a 900-foot bridge’s concrete and steel structures. The contractor had a niche business in surface treating small-to-medium-sized bridges. However, the work area on the riverbank beneath this bridge was especially difficult to reach. Furthermore, the work area was too small to fit most portable vacuum and recycling systems, in addition to power and air generators. As a final concern, the riverbank was unstable; too much weight concentrated in one area could cause it to collapse.
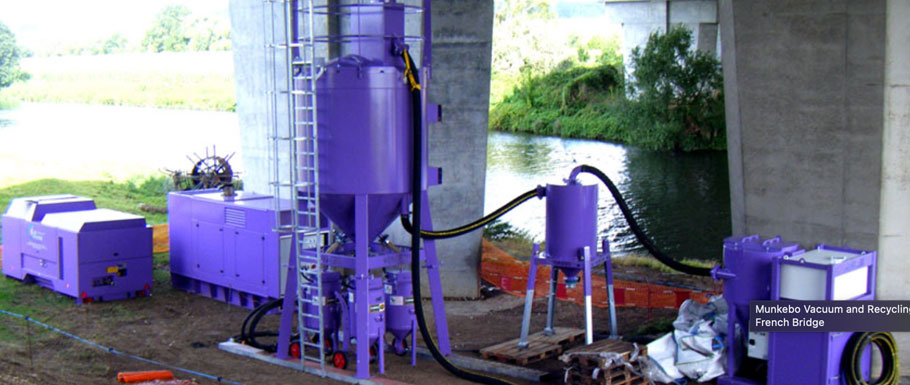
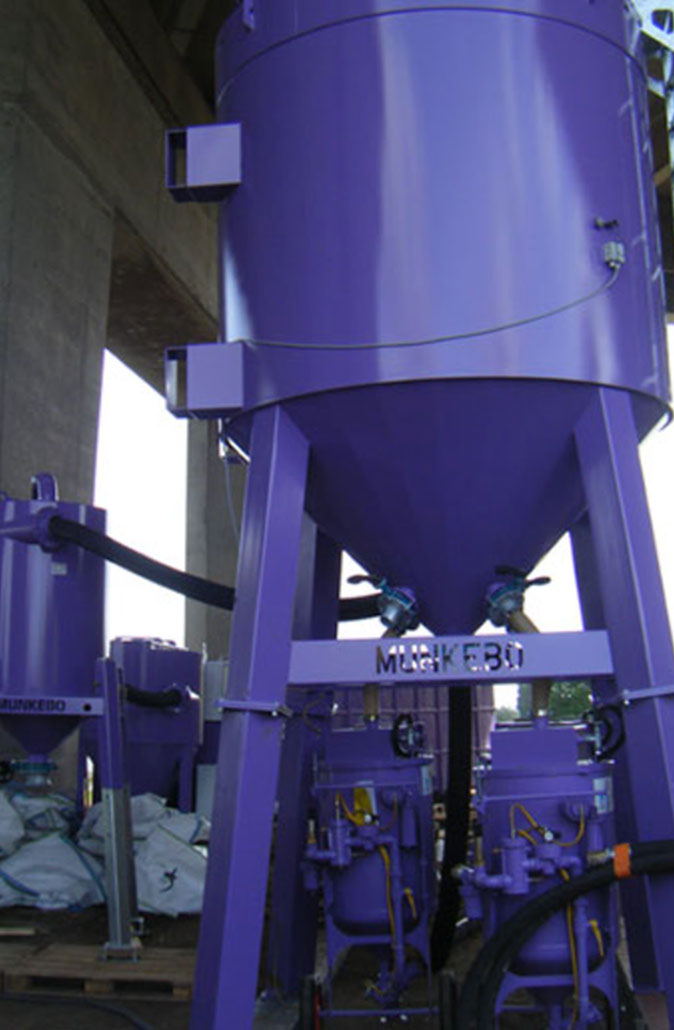
SOLUTION
The contactor purchased an MB-2000 Vacuum System, which is a medium-sized vacuum system that comes with an integrated cartridge filter. The contractor also purchased an additional cyclone separator and a 25-ton storage hopper with a custom-engineered air-wash system installed above the hopper. This vacuum and recycling system met the contractor’s needs for the following reasons:
- Space under the bridge was insufficient for a stand-alone recycling system, so Munkebo installed the air-wash system above the storage hopper. The air-wash system removed fines and dust from the spent steel grit before the grit entered the storage hopper.
- After the hopper was filled with the recycled steel grit, it could simultaneously refill up to four blast machines.
- Because of Munkebo equipment’s modular design, the contractor could configure the system’s components into the space restrictions of the work area while also distributing the weight of the equipment so that the riverbank remained stable.
- Even with the space savings and balanced weight distribution achieved by the equipment’s configuration, only enough space was safely available for lightweight power and air generators.
- Because Munkebo Vacuum and Recycling Systems are electric-powered, it takes less energy to run them than comparable diesel-powered equipment. This advantage allowed the contractor to use smaller generators that did not create instability on the riverbank.
- Likewise, because Munkebo equipment is electric-powered, lighter Munkebo equipment with smaller footprints often can accomplish the same jobs that would require larger and heavier diesel-powered equipment.
- The smaller footprint of the Munkebo equipment also enabled the vacuum and recycling system purchased for the job to easily fit on a standard-sized truck. No special rigging or tie-downs were needed to secure it, and light cranes easily removed and reloaded the equipment from the truck to the work area.
OUTCOME
The successful results at this job helped the customer grow its niche even further in small-to-medium-sized bridge surface treatment, and it has since purchased more Munkebo equipment.
Abrasive blasting (formerly known as sandblasting) also is called grit blasting, bead blasting, media blasting, soda blasting, dry blasting, sponge blasting, shot blasting, and shot peening. However, sand should never be used when abrasive blasting because breathing abrasive containing crystalline (free) silica can lead to serious or fatal lung disease.