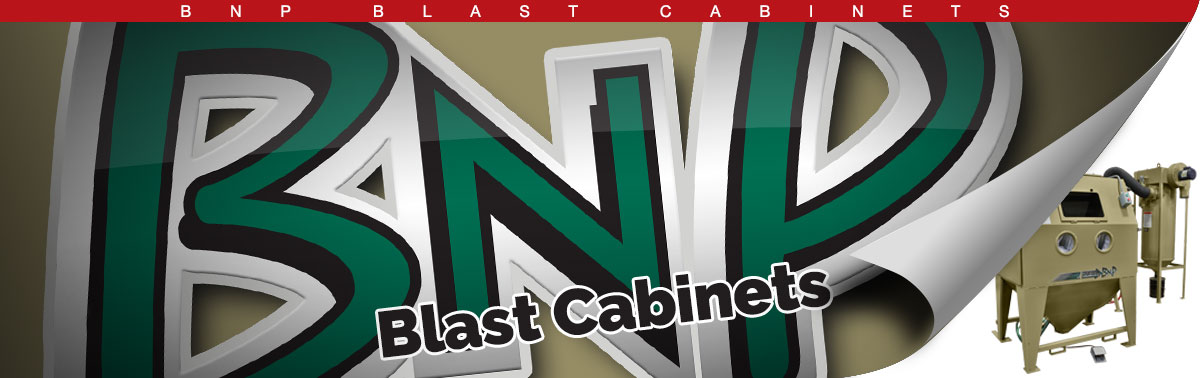
Abrasive blasting has been a critical part of industrial manufacturing and production operations for many years, and today the demands for greater performance, versatility and user safety of blast cabinets have never been greater. Using our unmatched understanding of abrasive blasting applications, Clemco has designed and engineered our line of BNP Blast Cabinets to provide high quality and customized abrasive surface preparation solutions for manufacturers and contractors serving a variety of industries including aerospace, power generation, oil & gas, firearms, medical, food services and others.
BNP Blast Cabinets deliver the high performance, efficiency and versatility needed for manufacturers to get the most out of their operations, production team and investment.
Productivity
Don’t let abrasive blasting slow your manufacturing production. BNP Blast Cabinet solutions help manufacturers reduce the cost and adverse impact of inconsistent part quality, unscheduled maintenance and equipment that is difficult to use and maintain. Our blast cabinets are designed to deliver consistent and repeatable results to your application while reducing downtime and keeping operators safe and productive. We ensure efficient operations by utilizing:
- Intuitive, accessible controls for easy use, including foot pedal for hands-free blast activation, regulator for blast pressure adjustment, and valve for media flow management.
- Modular components for easy access to routine maintenance for wearable components. Abrasive blasting naturally wears out components within the blast system. Ensuring that those components are durable and easily replaceable is key to reducing downtime.
- 50W LED Lighting for superior visibility while blasting.
Performance
Underperforming equipment costs you time and money. Our blast cabinets deliver consistent and high-quality abrasive blasting results that enhance quality and integrity in your production processes This means maintaining consistent nozzle pressure and media flow, proper media working mix, and optimal air flow through the system. BNP cabinets deliver this performance with:
- The BNP Suction Blast Gun, which sets the industry standard for high performance for Suction Systems.
- 2cf Capacity, ASME coded pressure vessel for maximum performance with Pressure Blast systems.
- High performance reclaim systems that are adjustable so you can fine tune media mixture.
- Reverse Pulse Dust Collectors that ensure you have the airflow needed through the system to increase visibility in the cabinet and keep your reclaim system working at maximum efficiency.
Versatility
The available space for abrasive blasting equipment in a production setting often requires working around other existing equipment or fixtures within the facility. You need a blast cabinet that has the flexibility to adapt into your environment and process while providing easy access to wearable components for preventative maintenance. BNP Cabinets solve the versatility challenge with:
- Modular components that enable the setup of blast cabinets to fit into your production line.
- Adaptable designs so your investment can grow with your business
- Seven different sizes of blast cabinets to accommodate the different size parts being blasted in your operations. BNP Blast Cabinets offer work chamber sizes ranging from 42” x 23” x 30” to 69” x 70.5” x 63” for Suction Blast systems and from 36” x 35” x 37” to 69” x 70.5” x 63” for Pressure Blast systems.
Suction and Pressure Blast Cabinet Models Available
BNP Blast Cabinets are available to support different types of blast technologies, including suction and pressure blast systems.
Suction Blast Systems use air and venturi to create a vacuum to pull media into the blast stream, which is then propelled out through the nozzle. These systems operate with lower air volumes than pressure systems.
Pressure Blast Systems use a pressurized vessel to deliver media to the nozzle. This can increase the blast production rate by as much as 300% when compared with suction blasting. These systems utilize higher air volumes than suction systems.
• BNP Suction Blast Cabinets Technical Data Sheets
• BNP Pressure Blast Cabinets Technical Date Sheets
Engineered Solutions
We will work directly with you to develop customized solutions to your specific abrasive blasting and cabinet needs and strengthen the overall performance and efficiency of your production operations. Want to learn more?
Abrasive blasting (formerly known as sandblasting) also is called grit blasting, bead blasting, media blasting, soda blasting, dry blasting, sponge blasting, shot blasting, and shot peening. However, sand should never be used when abrasive blasting because breathing abrasive containing crystalline (free) silica can lead to serious or fatal lung disease.