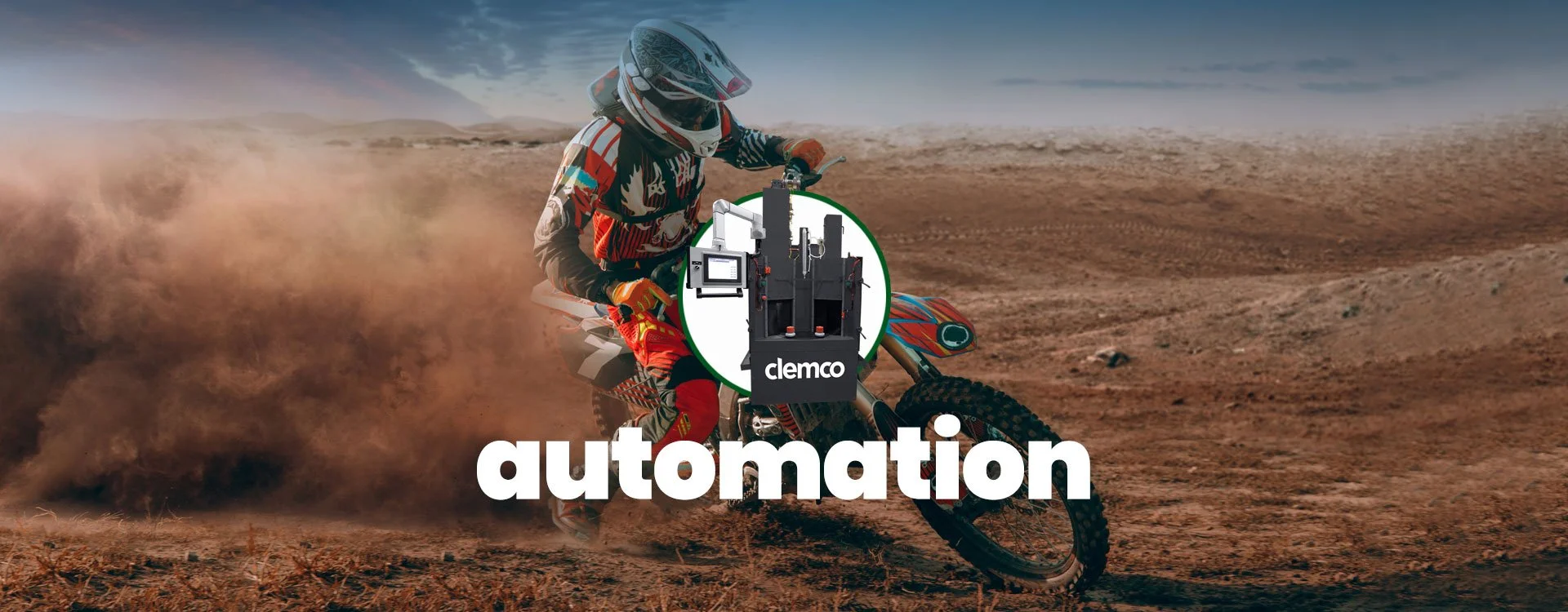
Automation
Clemco
Automation Integration
-
Job-to-Be-Done Engineering Approach: Clemco designs every solution—blasting, cleaning, or peening—by first deeply understanding the functional goal, part material, geometry, and performance requirements of the customer’s specific application.
Application-Specific Media & Method Selection: Whether it's achieving a precise Ra finish, removing coatings, or delivering controlled compressive stress for fatigue life extension, Clemco selects the optimal abrasive media, delivery method, and pressure to meet the target outcome.
Modular Systems Customized for Fit & Function: From portable blast machines to custom cabinets and automated blast rooms, Clemco configures systems based on throughput needs, part handling methods, and space constraints to match the workflow.
Industry-Specific Expertise: Clemco draws from decades of experience serving industries like aerospace, defense, automotive, oil & gas, and energy to tailor blasting and peening processes that meet sector-specific standards (e.g., AMS, SSPC, MIL-SPEC).
End-to-End Validation and Support: Every system is tested, validated, and supported with training and documentation to ensure it achieves the intended surface preparation result—from lab samples to production scale.
-
Clemco strength starts with an expansive range of core equipment and technologies for surface preparation:
Abrasive Blasting Systems: Portable blast machines, blast cabinets, blast rooms.
Shot Peening Systems: Controlled applications for fatigue resistance and surface improvement.
Dust Collection & Containment: High-efficiency systems to maintain safety and cleanliness.
Personal Protective Equipment (PPE): Helmets, respirators, suits, and communication systems.
This extensive baseline allows Clemco to configure modular or completely bespoke solutions tailored to customer applications in industries like aerospace, energy, defense, automotive, and heavy manufacturing.
Allen-Bradley HMI
-
Customizable Integration: Clemco automation solutions seamlessly integrate with both blast cabinets and blast rooms, enabling precise control over nozzle movement, part handling, and blast parameters. This flexibility boosts throughput and process consistency across varied applications.
Enhanced Safety and Ergonomics: By minimizing operator exposure to abrasive environments, automated systems reduce the risk of injury and fatigue—particularly valuable in high-volume or hazardous settings such as aerospace, defense, and energy sectors.
Repeatable, High-Quality Surface Prep: Automation ensures uniform blast patterns, dwell times, and media flow, consistently delivering surface preparation that meets stringent requirements for coating, bonding, and finishing.
Smart System Controls with Advanced UI: Clemco’s automated solutions feature integrated PLC/HMI platforms with user-friendly interfaces tailored for operator clarity and control. These systems support sensor feedback, data logging, and real-time diagnostics—empowering users to monitor, adjust, and optimize processes with confidence.
Scalable for Any Operation: From retrofitting existing blast equipment to engineering fully enclosed automated rooms, Clemco’s automation solutions are designed to scale—serving everything from R&D environments to large-scale industrial production facilities.
-
Clemco Delivers Custom Solutions for Specialized Part Handling and Automation, Optimizing Your Production Process Without Disruptions.
Fanuc Industrial Robotics
-
Seamless FANUC Integration: Clemco partners with FANUC Robotics to integrate advanced, programmable robotic arms into both blast cabinets and blast rooms, enabling precise and repeatable surface preparation for complex geometries and critical components.
Automated Nozzle and Part Manipulation: Robotic systems can either control the blast nozzle or manipulate the part itself, offering unmatched flexibility in processing diverse part sizes, shapes, and materials—ideal for aerospace, automotive, defense, and energy sectors.
Optimized Process Consistency and Quality: Clemco’s robotic solutions deliver uniform coverage, accurate dwell times, and consistent blast profiles, helping customers meet strict surface prep requirements while reducing rework and inspection failures.
Programmable Intelligence and Feedback Loops: Integrated FANUC controls with Clemco automation provide real-time diagnostics, adaptive feedback, and cycle optimization—making each blast cycle smarter and more efficient.
Safer, Smarter, Scalable Systems: Robotics eliminate manual operation in high-exposure zones, reducing injury risk and operator fatigue, while systems can be scaled from standalone cabinets to fully automated blast rooms in large-scale production environments.
-
Clemco Delivers Custom Solutions for Specialized Part Handling and Automation, Optimizing Your Production Process Without Disruptions.
KUKA Industrial Robotics
-
Automated Precision Blasting: KUKA robotic arms can be programmed to perform repetitive blasting tasks with exact motion control, ensuring consistent surface finishes, reduced variability, and improved part quality—ideal for aerospace, automotive, and defense applications.
Increased Throughput & Efficiency: Integrating robotics enables continuous operation with minimal downtime. KUKA robots can run multiple shifts without fatigue, dramatically increasing output in high-volume or high-precision production environments.
Enhanced Safety & Operator Ergonomics: By automating blasting inside enclosed cabinets or rooms, Clemco removes operators from direct exposure to abrasives, dust, and noise—meeting OSHA standards while improving workplace safety.
Flexible Multi-Axis Movement: KUKA robots offer 6-axis articulation, allowing them to reach complex geometries and confined spaces within parts—making them ideal for blasting turbine blades, structural welds, or intricate components.
Seamless System Integration: Clemco engineers can configure the robot to work with blast nozzle positioning, media flow control, ventilation, and reclaim systems—creating a fully synchronized, turnkey blasting cell with user-friendly touchscreen controls and real-time process monitoring.
-
Clemco Delivers Custom Solutions for Specialized Part Handling and Automation, Optimizing Your Production Process Without Disruptions.
-
Integrated Pick-and-Place Automation: Clemco systems can be engineered with robotic arms or gantries to handle pre-blast loading and post-blast unloading, enabling seamless transition of parts into and out of the blasting zone—minimizing manual labor and handling risks.
Upstream Part Identification and Orientation: Vision systems, sensors, and conveyors can be incorporated to identify, orient, and queue parts automatically before blasting, ensuring consistent part presentation and preparing mixed-part lines for efficient processing.
Downstream Finishing and Inspection: Robotic systems can continue beyond blasting to blow-off cleaning, media recovery, visual inspection, or automated sorting, reducing post-process bottlenecks and improving first-pass yield.
Closed-Loop Workflow Optimization: By linking blasting with upstream and downstream automation, Clemco creates smart, closed-loop systems that adapt in real time to part flow, cycle times, and quality metrics—boosting output while maintaining tight tolerances.
Labor Efficiency with Scalable Throughput: Engineered solutions reduce dependence on manual labor across the full process, allowing a smaller workforce to manage higher volumes with repeatable quality, especially in high-mix or high-precision environments.
-
Clemco Delivers Custom Solutions for Specialized Part Handling and Automation, Optimizing Your Production Process Without Disruptions.
Downstream & Upstream
Proven Performance. Rugged Reliability.
Generations of Excellence Transforming Our World, Worldwide since 1949
•
Generations of Excellence Transforming Our World, Worldwide since 1949
•
Generations of Excellence Transforming Our World, Worldwide since 1949
•
Generations of Excellence Transforming Our World, Worldwide since 1949 • Generations of Excellence Transforming Our World, Worldwide since 1949 • Generations of Excellence Transforming Our World, Worldwide since 1949 •
