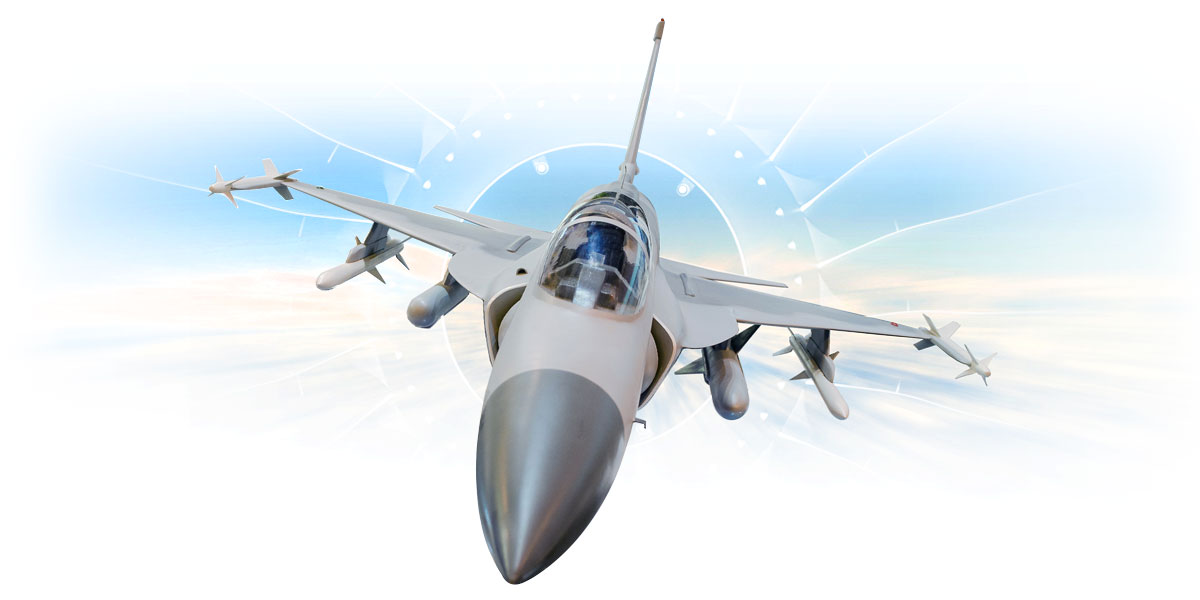
For More Information
If you’re seeking comprehensive solutions for your Aerospace needs, look no further than Clemco Aerospace Solutions. Simply complete the brief form below and our team of experts will promptly reach out to you.
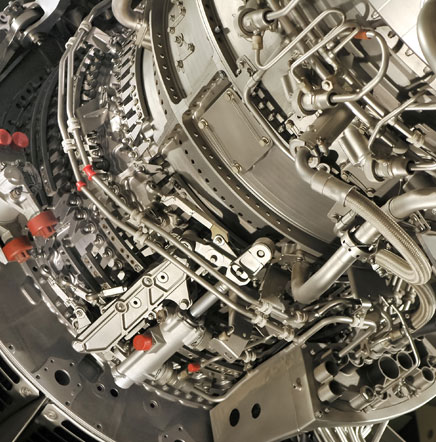
CASE STUDY 1:
Clemco Blasting Cabinet with Jib Crane and Smart Tech Enhances Airplane Maintenance
This customer blasts large airplane turbine engine components but has difficulty loading and unloading parts in their tight footprint. Clemco specifically tailored this 5’x5’ cabinet for blasting in this application. …
As the mounted jib crane and hoist efficiently load parts onto a swing-arm turntable. The low-pressure capable blast machine accommodates various tasks such as cleaning and coating stripping, easing the burden of diverse job requirements. Smart elements like blast pot level sensors and media screening minimize downtime by ensuring optimal blasting conditions. The advanced dust collection system not only extends maintenance intervals with a 55-gallon waste drum but also streamlines operations through automated pulse controls and closed-loop airflow regulation. These customer-centric features alleviate operational challenges, making the cabinet a solution that precisely addressed these unique pains.
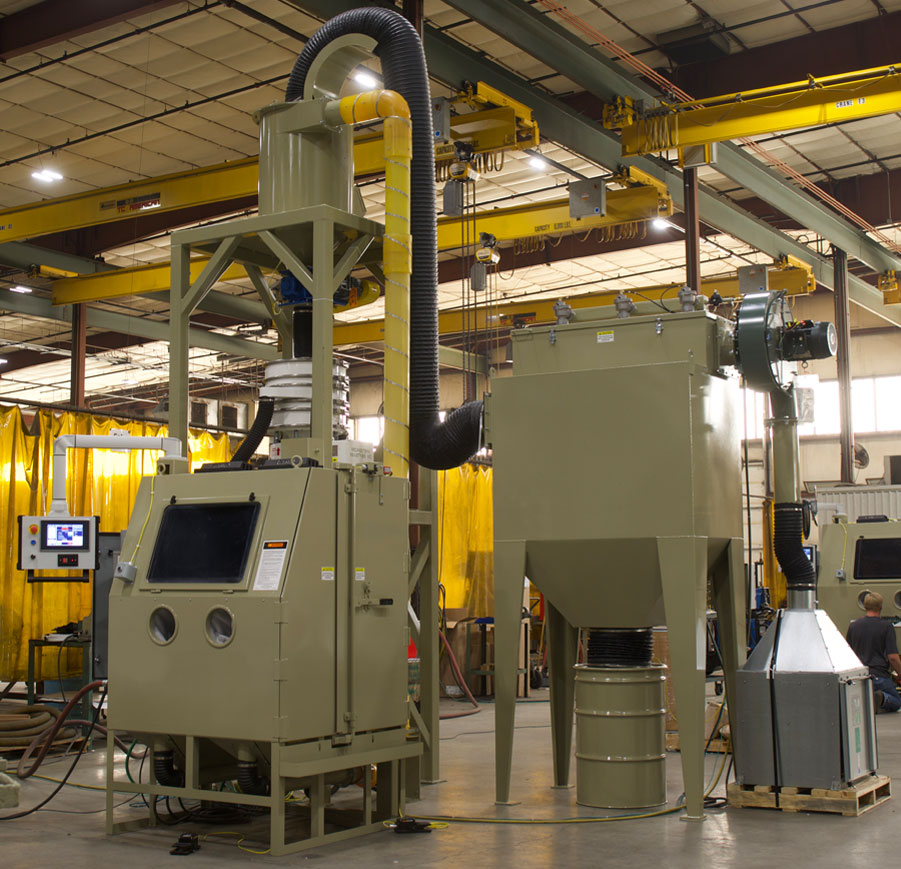
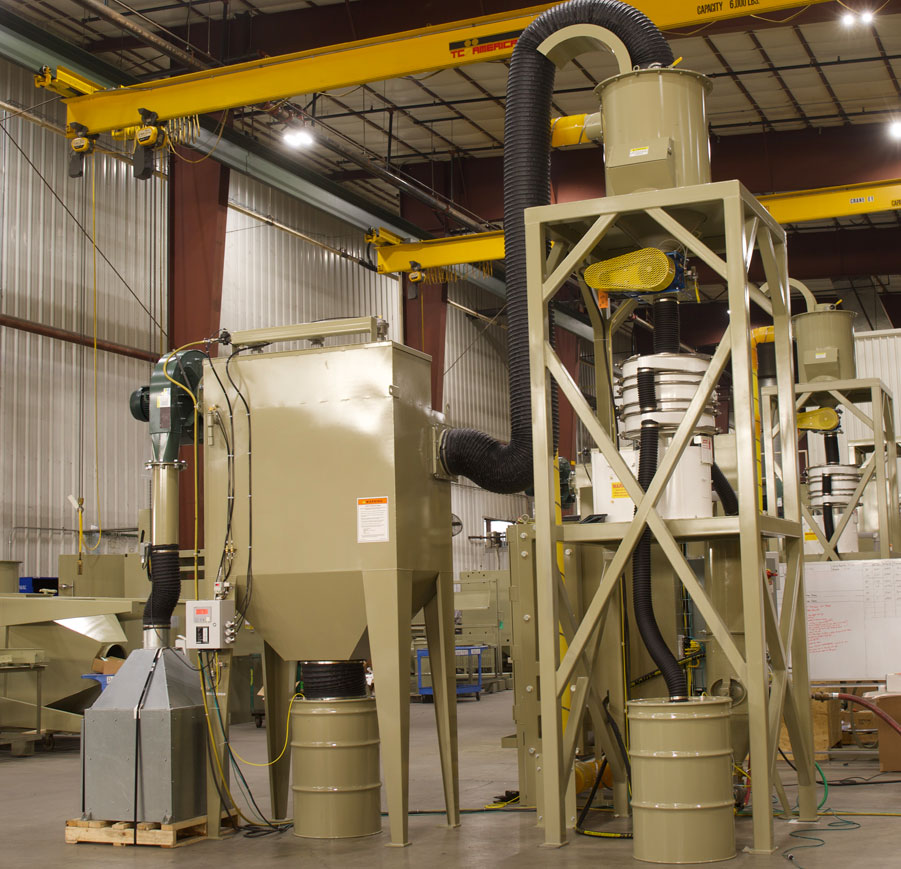
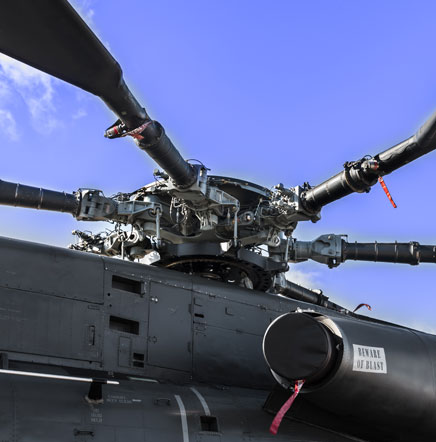
CASE STUDY 2:
Advanced Shot Peening System Enhances Helicopter Blade Maintenance with Improved Precision and Reduced Scrap
This customer specializes in shot peening of helicopter rotor blade components to enhance strength, a practice ingrained over decades with stringent specifications. …
To streamline their operations, we developed a seamless system, ensuring minimal downtime by serving as a direct replacement for their existing equipment. Our solution not only adheres to their precise process requirements but also introduces enhanced controls and data capabilities. This empowers them with greater control over the peening process, ultimately reducing scrap and rework. Additionally, the upgraded system facilitates improved tracking, bolstering quality control measures. This innovation aligns with their longstanding practices while elevating efficiency and precision in their operations.
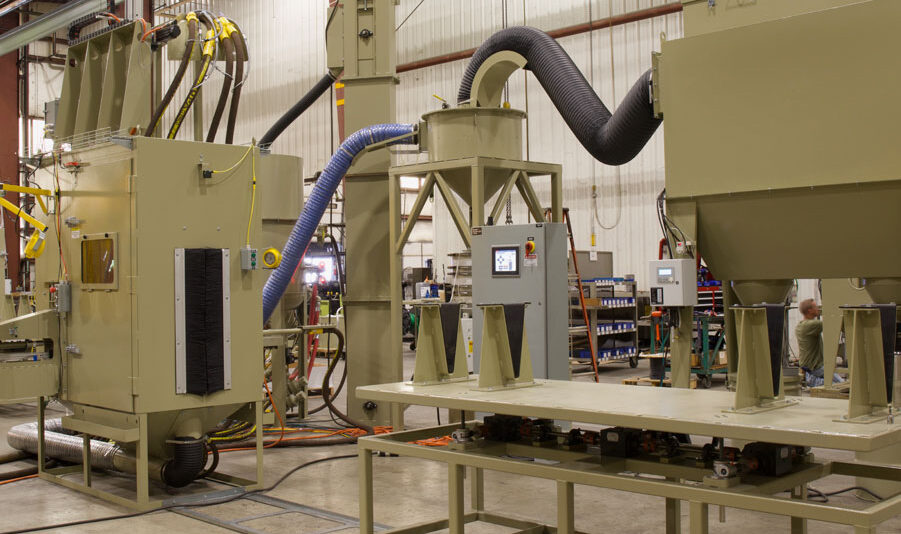
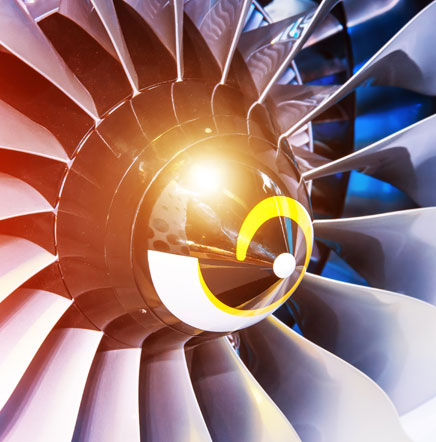
CASE STUDY 3:
Innovative Turntable System for Precision Blasting of Large Turbine Components: Enhancing Access and Control
Specializing in blasting large turbine engine components, our client faced a significant challenge due to a part with a substantial circumference, creating difficulties in reaching specific blasting areas …
In response, we innovated a solution: a turntable system that seamlessly rotates with a foot pedal and lifts the part into various angles. This design grants operators easy access to critical blast zones. Given that only specific areas require blasting, this targeted approach minimizes overspray into non-target areas. Our turntable not only addresses the pain point of limited accessibility but also enhances precision, ensuring efficient and controlled blasting processes for optimal results.
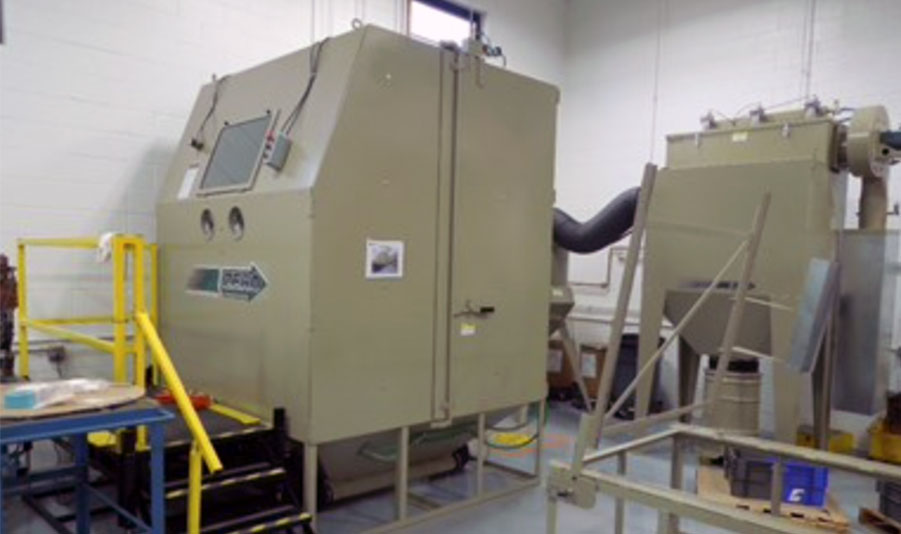
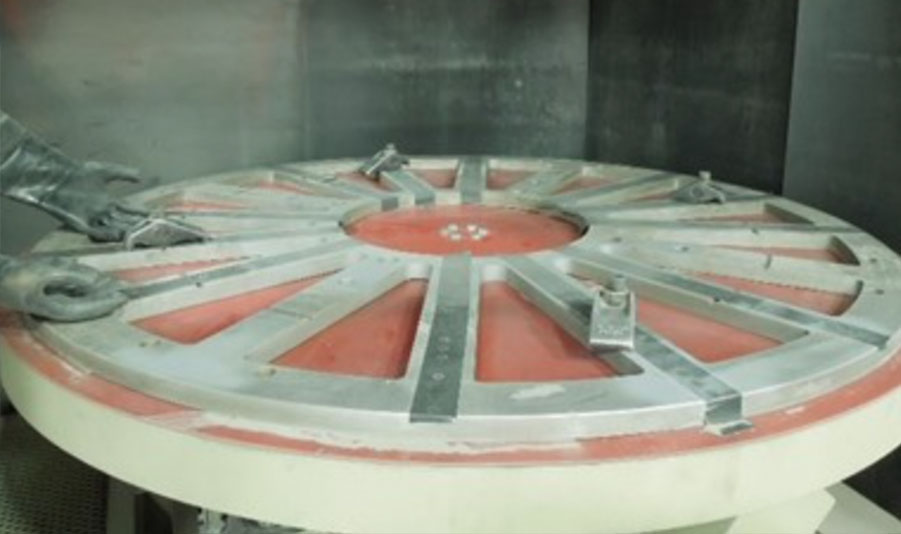
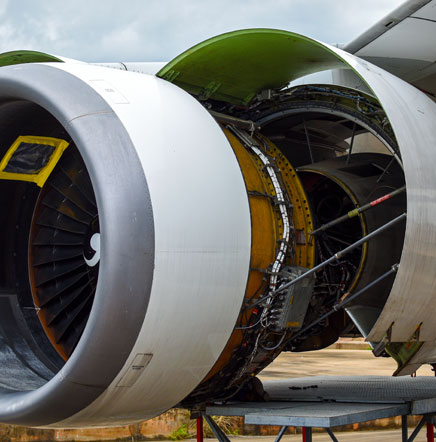
CASE STUDY 4:
Jet Turbine Blast System with Precision Tracking for Quality Assurance helps customer meet NADCAP requirements
In this application, the customer employs blast equipment to prepare jet plane turbine engine cowl components. Stringent quality tolerances demand a highly precise and trackable blast process. …
Achieving compliance with NADCAP certification standards is imperative. Our solution involves a sophisticated and robust system with an array of controls and blast capabilities. These components meticulously track and ensure the functionality of each stage of the process. This ensures that parameters are consistently met, aligning with the rigid quality standards. The integration of advanced controls with high performance blasting not only ensures precision but also establishes a robust foundation for maintaining the highest quality and efficient operations.
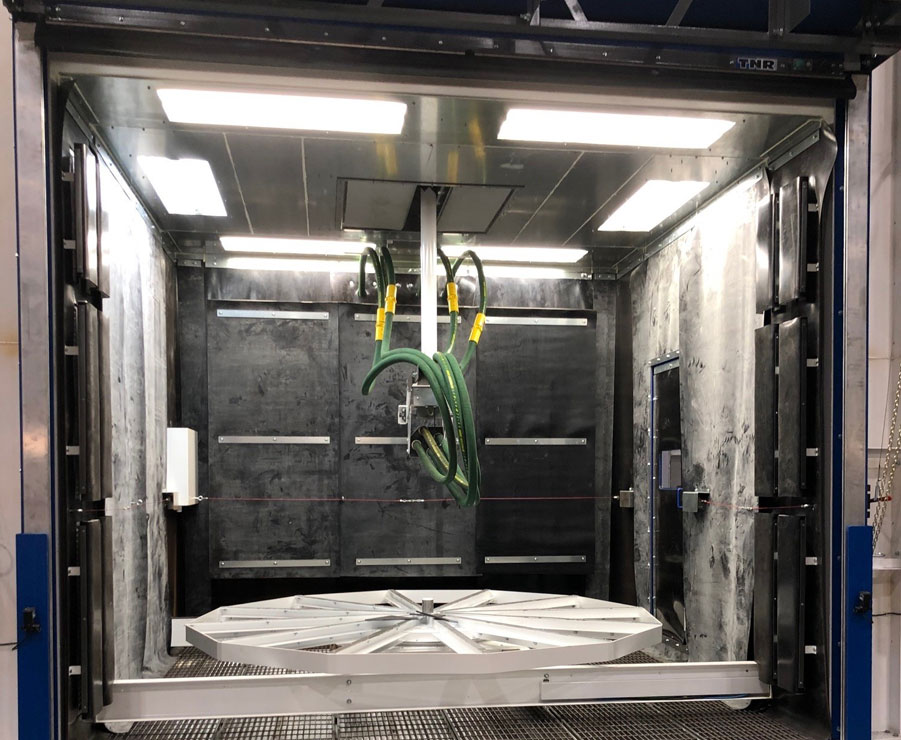
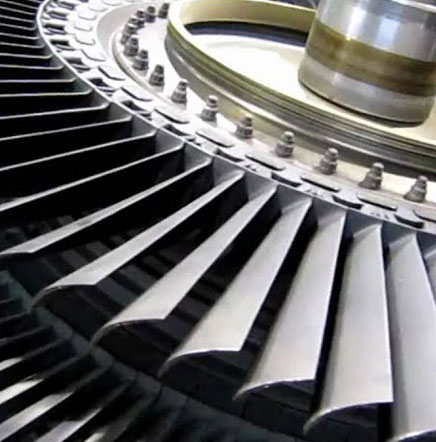
CASE STUDY 5:
Cabinet for Turbine Blades with Crane Slot, Turntable, Advanced Dust Collection for Space Efficiency in MRO applications
This 4’W x 4’D cabinet, designed with an extended height, tackles specific customer challenges in blasting tall turbine engine blades, where pain points demand innovative solutions. …
Featuring a crane slot and an internal turntable, it addresses the difficulty of loading especially tall parts using an overhead crane within tight spatial constraints. Departing from the conventional workcars on tracks, this cabinet’s inventive crane slot significantly reduces the enclosure’s footprint. Customized for stripping coatings off turbine engine blade ends for meticulous MRO inspection, the low-pressure plastic blast machine ensures thoroughness. Blast pot level sensors mitigate operational hurdles, preventing time wastage and simplifying startup checks. The advanced dust collection system, incorporating a 55-gallon waste drum, automated controls, and closed-loop airflow regulation, confronts unique challenges head-on, extending maintenance intervals and maximizing efficiency in media reclaim and cleaning results.
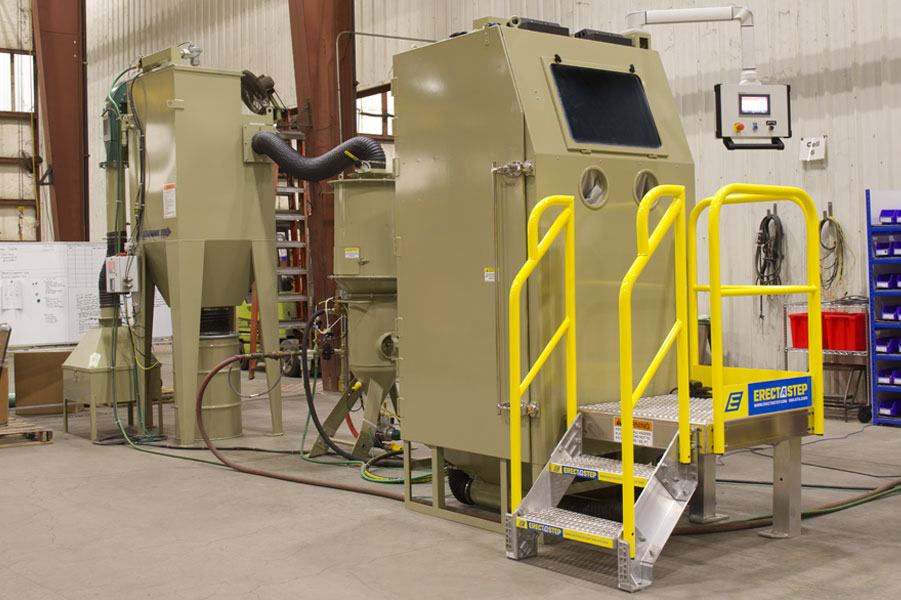
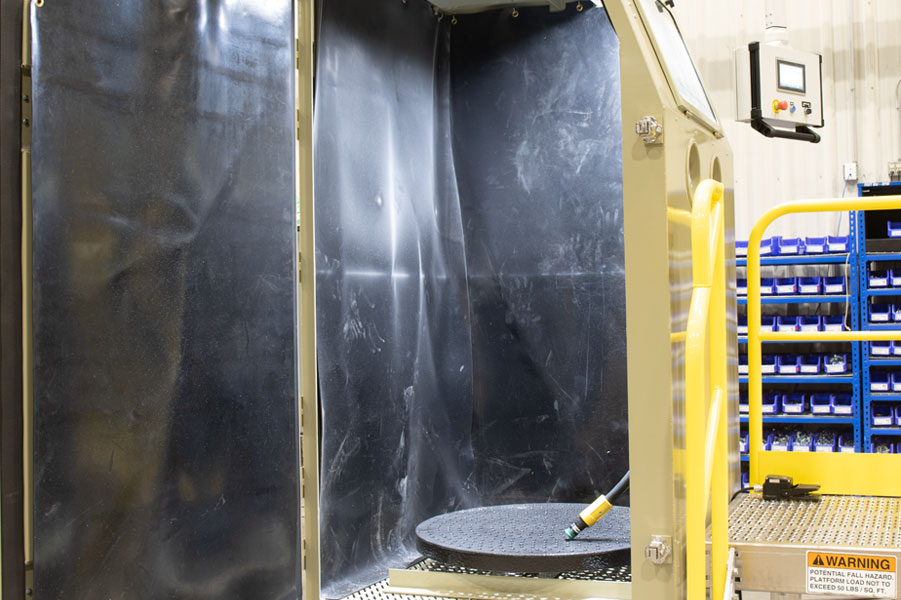
Abrasive blasting (formerly known as sandblasting) also is called grit blasting, bead blasting, media blasting, soda blasting, dry blasting, sponge blasting, shot blasting, and shot peening. However, sand should never be used when abrasive blasting because breathing abrasive containing crystalline (free) silica can lead to serious or fatal lung disease.