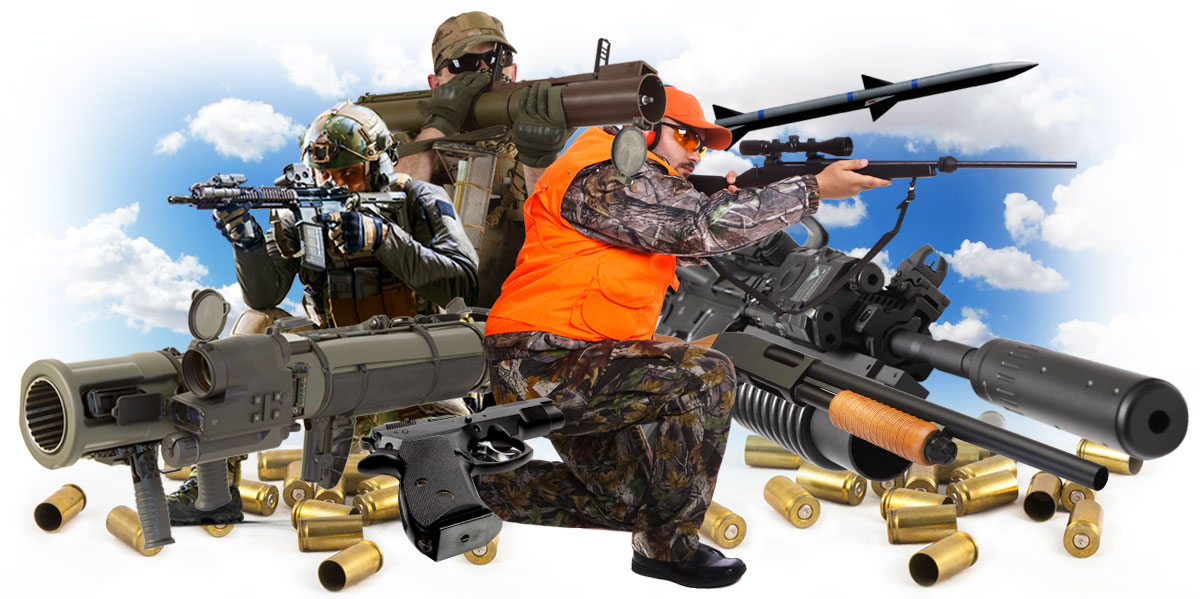
For More Information
If you’re seeking comprehensive solutions for your Firearm needs, look no further than Clemco Firearm Solutions. Simply complete the brief form below and our team of experts will promptly reach out to you.
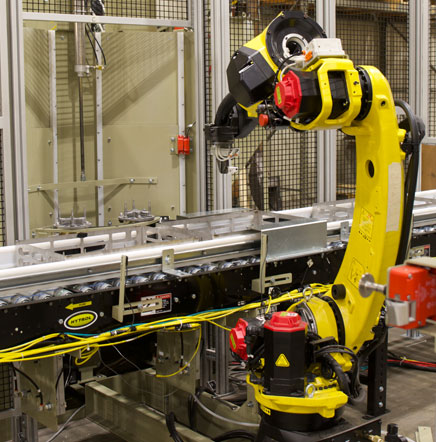
CASE STUDY 1:
Robotic Load/Unload System Increases Handgun Slide Production Volume and Lowers Costs
Our customer was seeking a way to boost production volume and lower costs when manufacturing handgun slides, a process which can be difficult to keep up with due to its many steps from cleaning to coating. …
Our solution: a robotic load/unload indexing cabinet with a PLC, HMI, and vertical oscillation blasting. This system eliminates the need for carts and manual part handling, reducing part handling by up to four times. Three slides can be blasted simultaneously, tripling the throughput of the process. Predictive maintenance, reporting, metrics, and troubleshooting information further increase efficiency and safety.
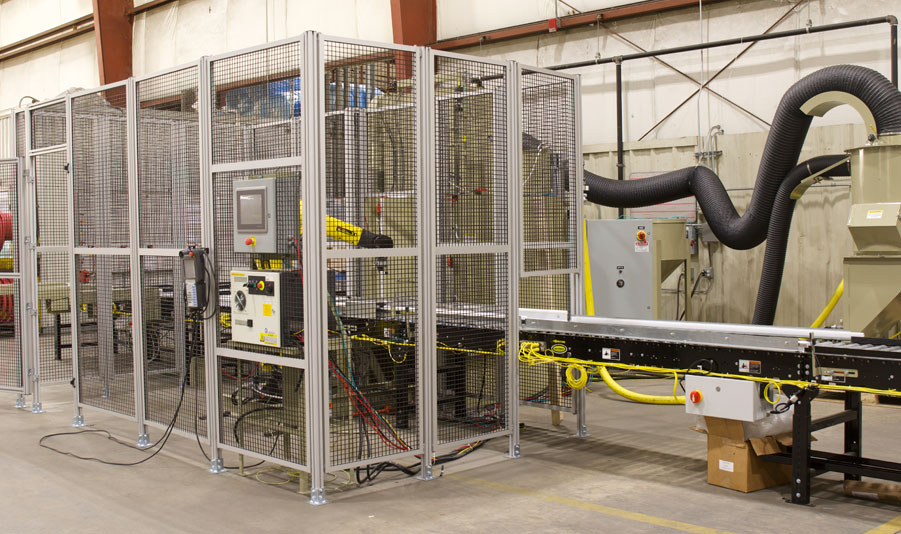
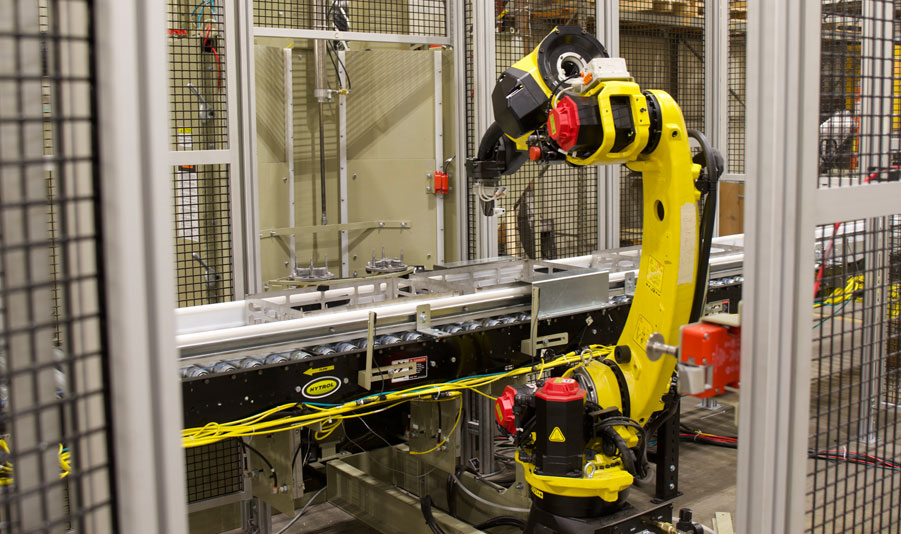
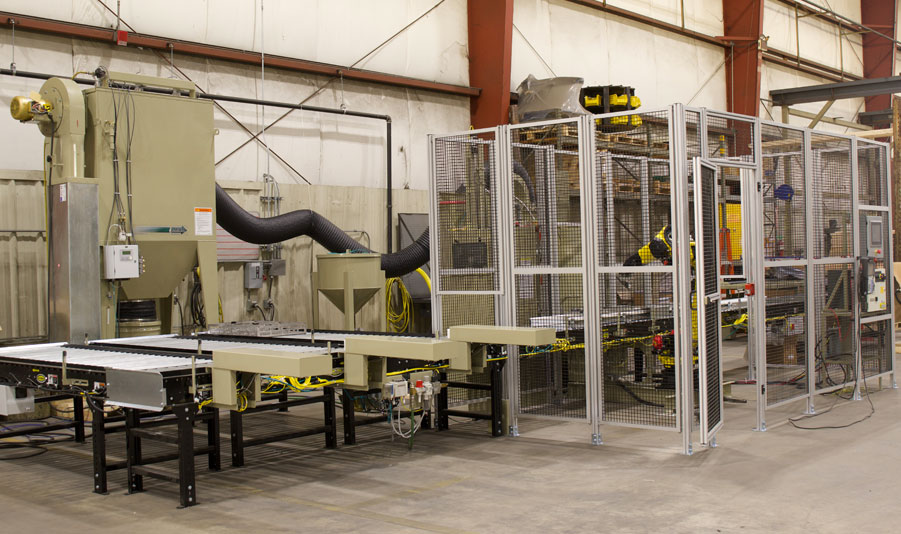
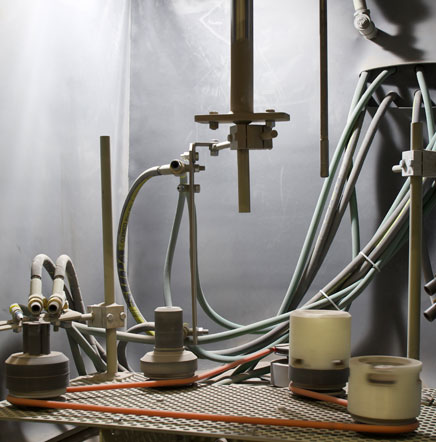
CASE STUDY 2:
New Automated System Transforms Firearm Assembly, Reducing Costs and Improving Productivity
The implementation of a new automated system for the assembly and blasting of four components of a firearm assembly greatly reduced costs and improved productivity for our customer. …
This system, consisting of two vertical oscillators and four rotating satellites, allowed for a more precise profile while reducing operator interaction. The results of this new system have been impressive: media usage was reduced by 5%, scrap and rework decreased by 50%, and labor efficiency increased by 250%, with only one operator now needed to assemble and blast the four components. The capital investment for this new system was paid back within ¼ of a year, making it a highly cost-efficient solution that has transformed our customer’s operations.
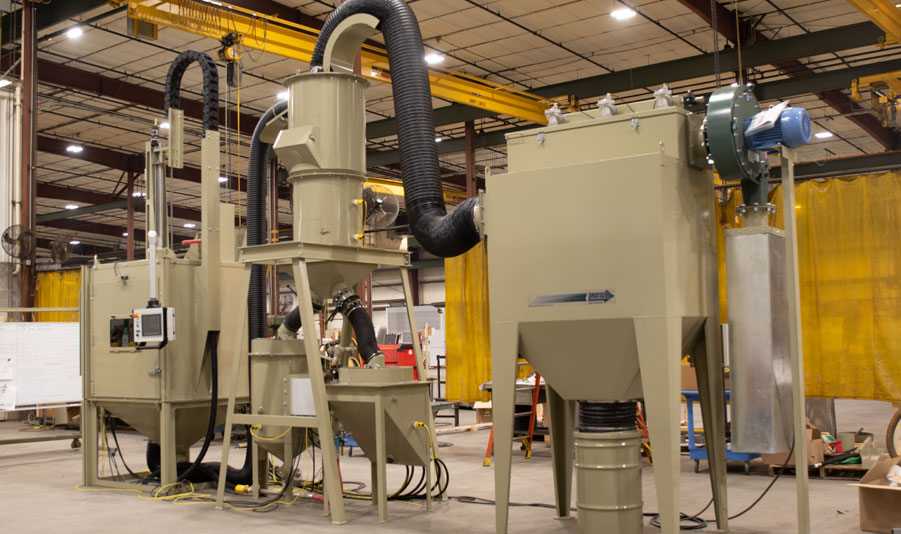
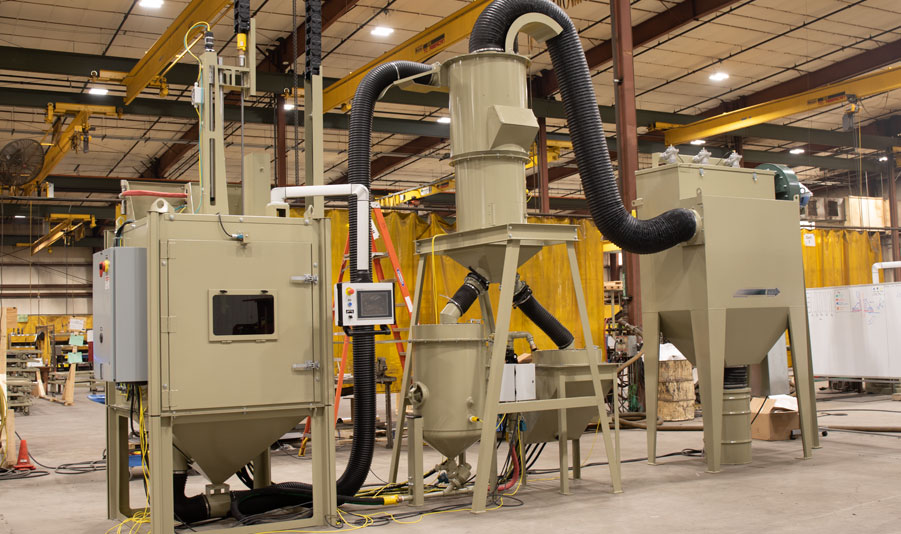
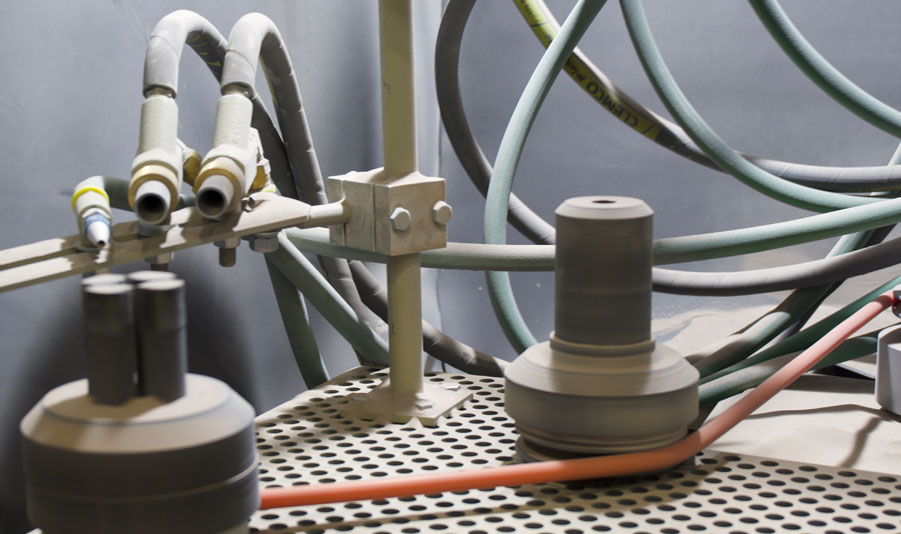
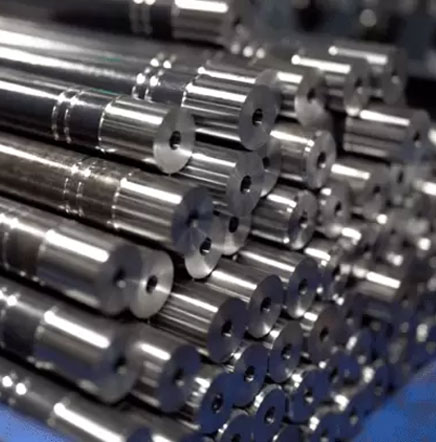
CASE STUDY 3:
Revolutionizing Production of Rifle Barrels and Receivers with Single Large Indexing Cabinet
Our customer was having difficulty producing finishes for rifle barrels and receivers that ranged from 20” to 36” in length on time. Their existing setup was inadequate, …
Their existing setup was inadequate, with multiple setups and changeovers, as well as two cabinets and two operators to handle odd sizes, leading to slower production and inconsistent finishes on large, odd-sized parts. To remedy these issues, we proposed a single large indexing cabinet with a PLC and HMI. This increased production capacity, decreased the number of necessary changeovers (fixtures, blast gun locations, blast pressure, stroke length, and part rotation) and improved the consistency of surface prep. It also freed up the second operator for other tasks.
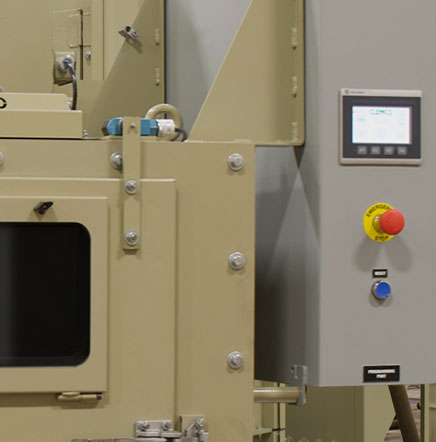
CASE STUDY 4:
Smart Tumble Cabinet System Delivers Efficiency and Cost-Effectiveness to Handgun Components Blasting Process
Our customer was blasting handgun components and looking for a way to increase efficiency and cost-effectiveness in their process. Unfortunately, their existing tumble cabinets weren’t up to the task, …
Unfortunately, their existing tumble cabinets weren’t up to the task, leading to increased downtime and excessive dust in the air and reclaim systems. This caused the parts to have to be tumbled longer to achieve the desired finish, and it also had the potential to reduce coating adhesion. To remedy this, we provided a tumble cabinet with a smart dust collection system and filter management. This allowed for better working mixes of media and consistent finish on the parts.
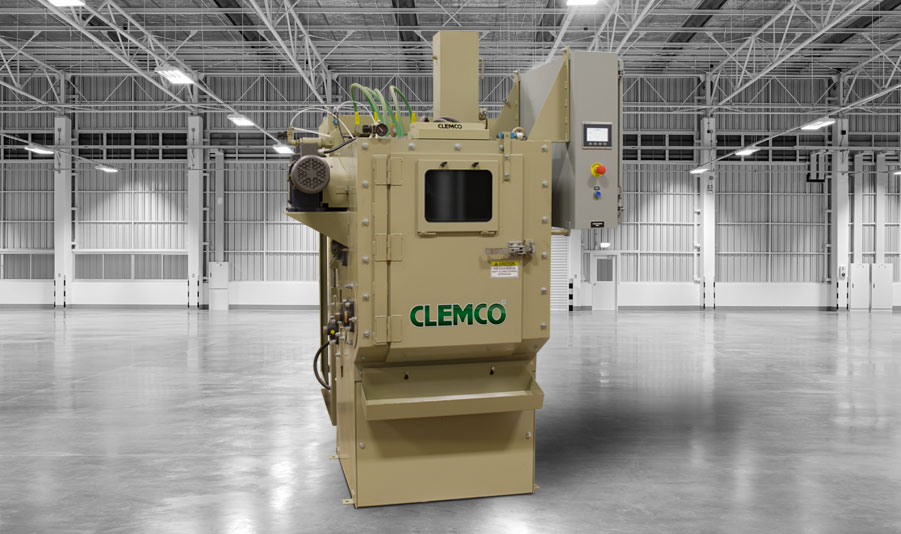
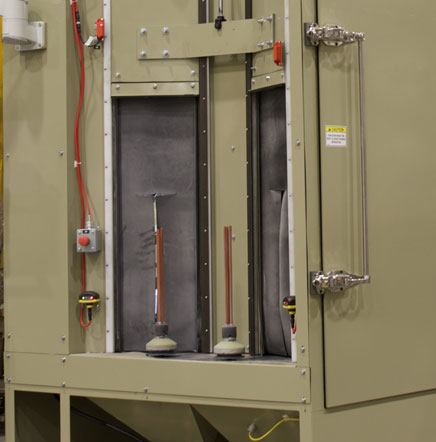
CASE STUDY 5:
Automated Indexing Cabinet Increases Efficiency and Consistency in Shotgun Barrel Coating
Our customer was looking for a reliable way to prepare shotgun barrels of lengths ranging from 15 to 32 inches for coating. The problem was that the old cabinet was not up to the task. …
It was composed of all relay logic and required hand configuration. The solution was to upgrade to an automated indexing cabinet. This automated indexing cabinet is equipped with a smart dust collector, a PLC, and an HMI, to reduce downtime, changeover time, and provide predictive maintenance. The result is a better and more consistent surface profile due to the improved air flow and media separation.
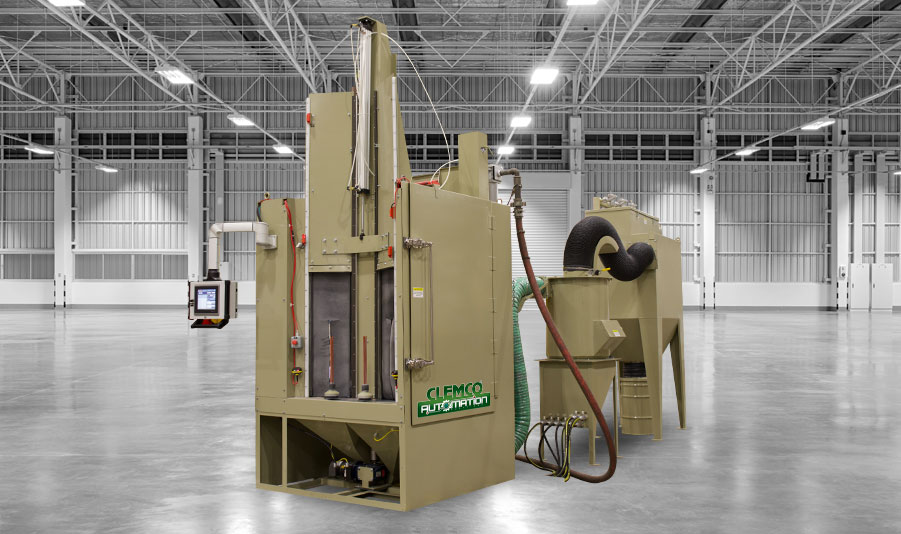
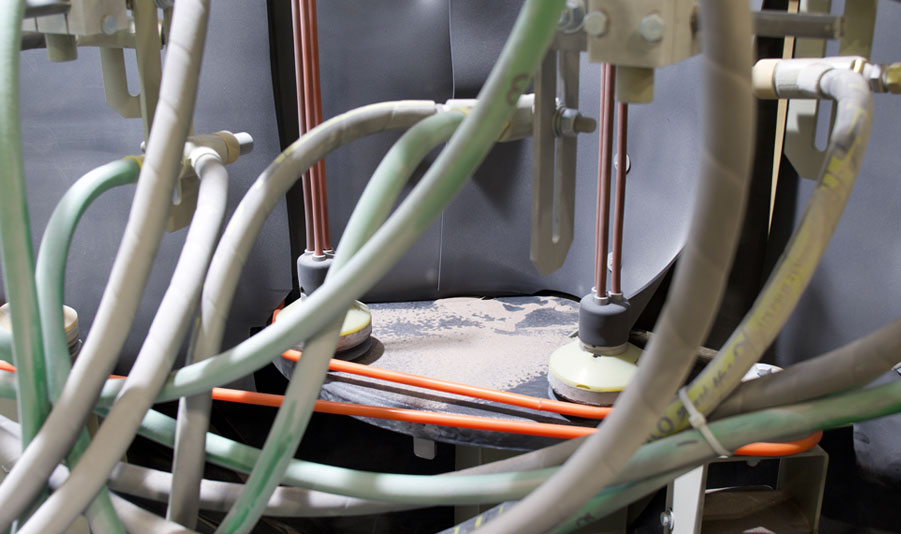
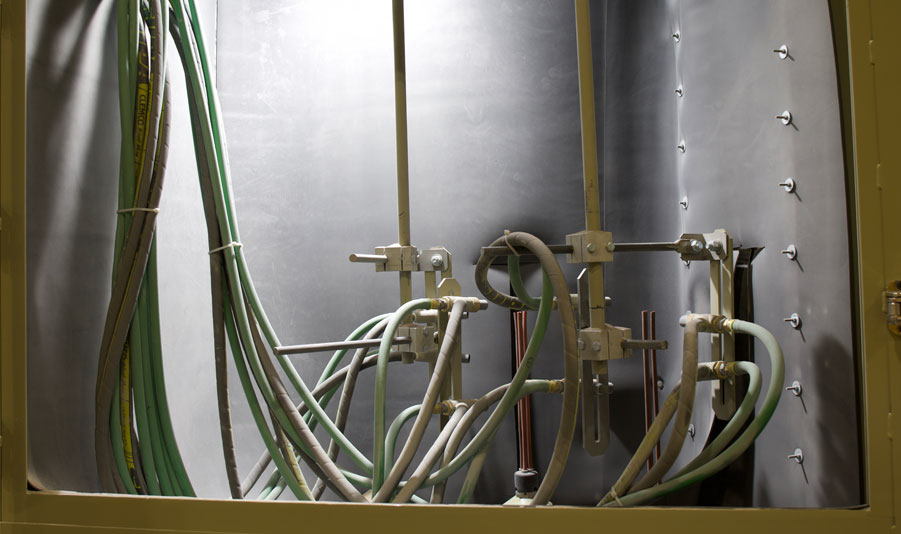
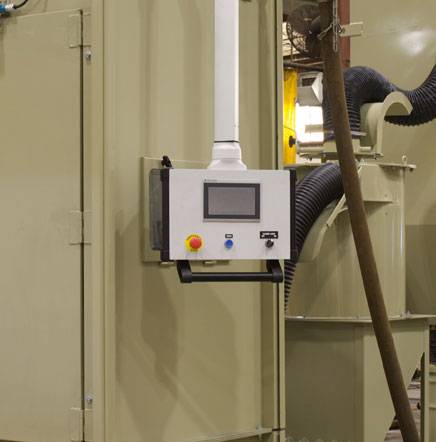
CASE STUDY 6:
Automated Blast Cabinets Cut Production Time In Half, Reducing Downtime and Scrap for Munitions Manufacturer
The customer struggled with a complicated two-step surface preparation process for munitions. It involved blasting the metal surface, then applying a composite coating, followed by a second blast of the coating. …
Different abrasives had to be used on different substrates, making the process difficult and limiting the number of liners that could be produced in a day. Moreover, the process was rigid, and changeovers were difficult, leading to costly downtime of up to four hours or more. To address this, we provided two automated blast cabinets with PLC and HMI, as well as a rotating satellite design with vertical oscillation for the length of the part. This allowed us to cut production time in half, while the cost of the two machines was relatively low compared to the downtime and scrap the customer was experiencing with the old process. The outcome was extremely successful, with minimal reworks, better surface preparation, no changeover, and a reduction in scrap.
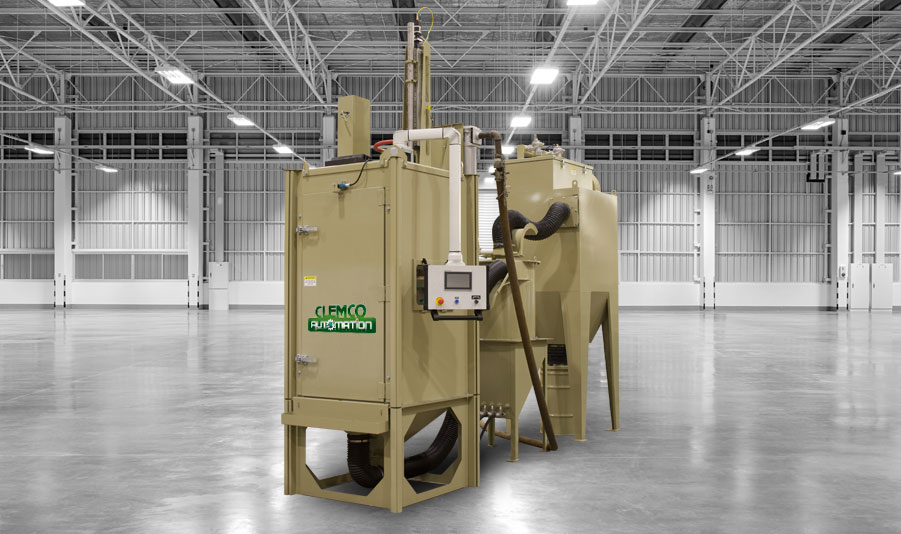
Abrasive blasting (formerly known as sandblasting) also is called grit blasting, bead blasting, media blasting, soda blasting, dry blasting, sponge blasting, shot blasting, and shot peening. However, sand should never be used when abrasive blasting because breathing abrasive containing crystalline (free) silica can lead to serious or fatal lung disease.