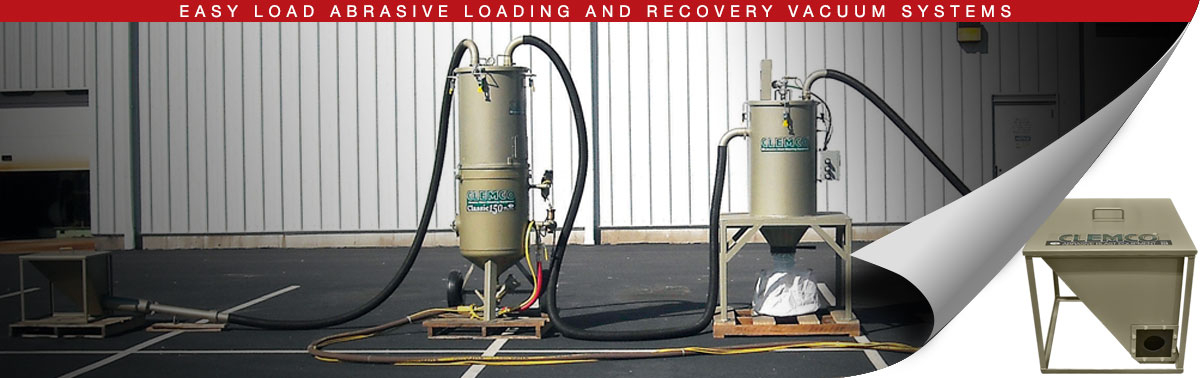
Loading new abrasive and sweeping up or shoveling used abrasive is backbreaking, time-consuming work that takes operators away from blasting.
Manually loading and recovering abrasive can take up to 50% of an abrasive blasting project’s time. It’s work that fatigues operators, making them less focused and productive, and it can lead to operator injuries and expose them to hazardous dust. It also takes operators away from the reason they are on the job site—to be blasting.
For these reasons, Clemco offers two Easy Load Abrasive Loading/Recovery Systems and one Easy Load Recovery System that all speed up your abrasive loading and recovery, boosting the productivity of your abrasive blasting operation while helping to contain dust and protect operators from injury.
ELS-2-290 – Low to Medium-Production Abrasive Loading or Recovery
- Operation – Vacuums up abrasive into a 6-cuft media storage hopper for either:
- Disposal or transfer to a recycling system.
- Loading the collected media into a blast machine placed underneath the hopper.
- System Components – In addition to a 6-cuft media storage hopper, the ELS-2-290 comes with a reverse-pulse dust collector and a media pickup tool that can be attached to an included media loading hopper.
ELS-4-290 – High-Production Abrasive Loading or Recovery
- Operation – Vacuums up abrasive into a 17-cuft media storage hopper for either:
- Disposal or transfer to a recycling system.
- Loading the collected media into a blast machine placed underneath the hopper.
- System Components – In addition to a 17-cuft media storage hopper, the ELS-4-290 comes with a reverse-pulse dust collector and a media pickup tool that can be attached to an included media loading hopper.
ELS-6-290 – Vacuums Up Abrasive for Disposal or Recycling
- Operation – Vacuums up abrasive into a 6-cuft collection container for disposal or for transfer to a recycling system.
- System Components – In addition to a 6-cuft collection container, the ELS-6-290 comes with a reverse-pulse dust collector and a media pickup tool.
Four Benefits of Clemco Easy Load Systems
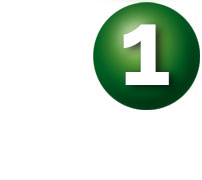
Simple Design and Small Footprint – Versatile, Efficient, Easy-to-Use Equipment
- Easy to Transport, Set Up, and Configure to Job Site Restrictions
- Easy Load Systems’ modular designs allows operators to easily configure the systems to fit onto trucks or trailers for transportation to job sites.
- Likewise, their designs simplify setup and allows for configuring Easy Load Systems to the space restrictions of different job sites.
- Vacuum Powered – Easy Load Systems’ vacuum power runs off an air compressor that you already have onsite to power your blast machines. No need to bring in additional equipment, saving money and space on the job site.
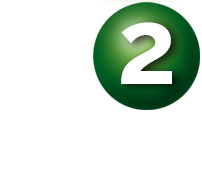
Integral, Reverse-Pulse Dust Collectors – Promote Safety and Productivity, Help Avoid Regulatory Fines
- Reduce Respiratory Hazards – Easy Load Systems’ reverse-pulse dust collectors automatically remove dust when they load or recover media, reducing respiratory hazards.
- Low-Maintenance, High Productivity
- You set the cycle time for the reverse-pulse dust collector’s jets of air, which automatically clean the dust collector’s filter cartridges.
- This automatic cleaning simplifies cartridge maintenance, prolongs the dust collector’s service life, and ensures consistent cartridge cleaning that helps maintain high productivity of the entire Easy Load System.
- Safer Than Manual Methods
- Sweeping and shoveling abrasive for cleanup creates respiratory hazards by stirring dust into the air, as does operators cutting open bags of abrasive and then pouring the abrasive into their pots.
- These activities put your operators and others in the area at risk of breathing hazardous dust.
- It also risks safety and compliance issues, which can cost you through fines and lost business.
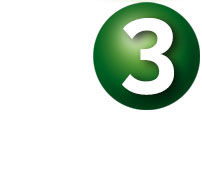
Less Time Loading and Recovering Media = More time for Blasting
- Inefficient Manual Abrasive Recovery – It’s impossible to get all media out of corners, cracks, and other hard to reach areas for recovery by sweeping or shoveling media.
- Inefficient Manual Abrasive Loading – Likewise, manually loading abrasive into blast machines is time-consuming, strenuous work that leads to operator fatigue and more spilled and wasted media.
- Safety and Compliance Risks – Spilled media during loading and uncollected media during recovery can lead to safety and compliance issues.
- Efficient Easy Load Systems
- Put simply, an Easy Load System is like a highly efficient, giant vacuum cleaner.
- Its pickup tool easily gets to where abrasive is lodged or hidden—places that would be nearly impossible to recover abrasive from manually.
- They also recover media or load it into a storge hopper much faster than manual methods.
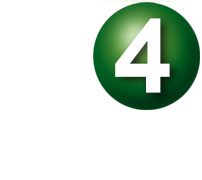
Low-Maintenance, High Productivity
- Minimal Wear and Ease of Maintenance – Easy Load Systems are designed for minimal wear and ease of maintenance with properly designed airflow and limited wear components, which keeps your crew working the job instead of working on their equipment.