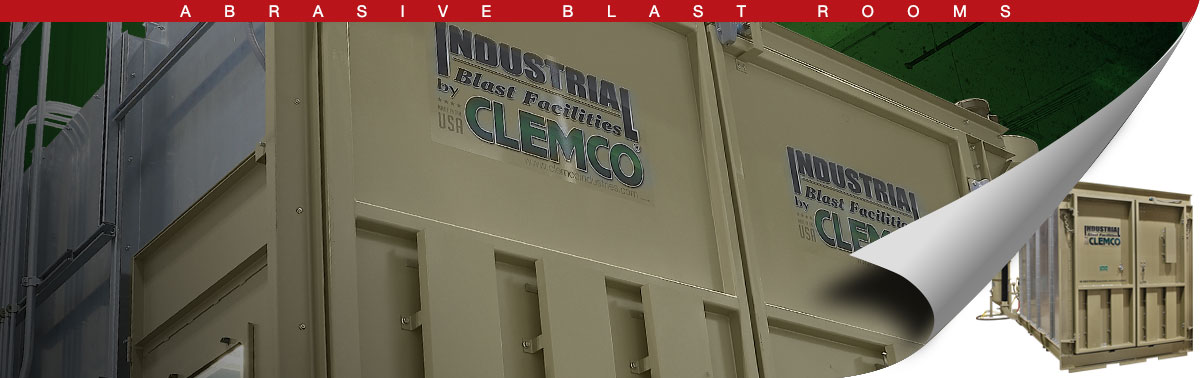
A Blast Room Tailored to Your Application Increases Productivity, Profits, and Safety
You abrasive blast in a room for three main reasons: containment, avoiding weather-related unpredictability from blasting outdoors, and media recovery. But if your blast room isn’t optimized to your application, you’re inviting productivity, maintenance, and safety issues.
For these reasons, Clemco offers three lines of blast room solutions, all completely engineered, designed, and manufactured in-house at Clemco’s corporate manufacturing and engineering headquarters in Washington, Missouri. Keeping the entire process in-house ensures that we supply safe, highly productive blast rooms that meet the requirements of your abrasive blasting application.
Preassembled Blast Rooms
Delivered to your facility ready to install. These compact, prebuilt blast rooms fit into tight footprints and need only air and power supplies to begin blasting.
- Dimensions – 14’L x 7’W x 8’H
- Sturdy Construction – 10ga galvanized steel wall and ceiling panels.
- Media Recovery Options – A Pneumatic M-Section Recovery System for lightweight media or a Mechanical Flat-Trak Recovery System for steel or other heavy and/or coarse media. Both systems can be installed in a pit or on top of an existing foundation.
- Media Cleaning – A 1,200 CFM cyclone reclaimer pairs with the M-Section Recovery System, and an air-wash abrasive cleaner (AWAC) goes with the Flat-Trak Recovery System.
- Reverse-Pulse Dust Collector – CDF-4 Dust Collector with 4,000 CFM capacity for high-volume blast room ventilation.
- Also Includes – PPE package, industrial 6-cuft blast machine package, and more.
Predesigned PDQ Blast Rooms
Offered in a variety of sizes and pre-configurations. Predesigned blast rooms provide flexibility for various footprints and a short lead time. They are delivered as bolt-together subassemblies designed for quick and easy installation.
- Dimensions
- Width – 10 ft or 12 ft
- Height – 8 ft, 10 ft, or 12 ft
- Length – Vary from 10 ft to 30 ft, depending on room width and height.
- Sturdy Construction, Quick Installation – 10ga galvanized, bolt-together steel wall and ceiling panels designed for quick and easy installation.
- Media Recovery Options – Choose either a Pneumatic M-Section Recovery System for lightweight media or a Mechanical Sweep-In Hopper Recovery System or steel or other heavy and/or coarse media. Both systems can be installed in a pit or on top of an existing foundation.
- Reverse–Pulse Dust Collector – A CDF-6 Dust Collector with 6,600 CFM capacity for 8 ft high blast rooms. A CDF-8 Dust Collector with 8,800 CFM capacity for 10 ft and 12 ft high rooms. Both systems for high-volume blast room ventilation.
- Also Includes – PPE package, industrial 6-cuft blast machine package, and more.
Engineered Blast Rooms
Purpose-built blast rooms engineered to accommodate your unique application requirements and processes. They usually are delivered to your facility as 10ga galvanized, bolt-together subassemblies designed for quick and easy installation.
- Satisfied Customers – Clemco has designed and manufactured engineered blast rooms to paint strip fighter jets for the U.S. Air Force, surface preparation of mining-truck frames before painting, cleaning welds on large stainless-steel tanks, and numerous other applications.
- Ideation to Realization (I2R™) – Clemco is not your typical quote-it, deliver-it, and forget-it vendor. During our six-phase I2R process, Clemco engineers collaborate with your team to uncover the true root cause or causes of your blast room challenges so that together we find a solution that solves the problems beneath the problem.
- Recovery Options –Belt conveyer, screw conveyor, sweep-in hopper, Flat-Trak, or M-Section to fit the media recovery requirements of your blast room’s applications.
- Integrated Options – Multi-axis manlifts, rail-mounted workcars, overhead monorails, and other systems can be integrated into your blast room to enhance workflow.
- Automation and Robotics – Clemco can integrate blast room solutions with the level of automation you need ranging from:
- Robotics for blasting and nozzle manipulation
- Touchscreen HMI with realistic graphic
- Automatic airflow-adjustment controls
- Information management such as cycle reports and efficiency statistic
- And much more
Abrasive blasting (formerly known as sandblasting) also is called grit blasting, bead blasting, media blasting, soda blasting, dry blasting, sponge blasting, shot blasting, and shot peening. However, sand should never be used when abrasive blasting because breathing abrasive containing crystalline (free) silica can lead to serious or fatal lung disease.